The 18th annual Reliable Plant Conference & Exhibition recently welcomed nearly 1,600 industry experts, leaders and decision-makers from around the world to the Greater Columbus Convention Center in Columbus, Ohio, for three days of learning and finding solutions to plant problems. The premier event for lubrication, oil analysis and reliability professionals drew delegates from 40 U.S. states and 28 countries, including groups of individuals from top organizations such as Cargill, Chevron, Citgo, Entergy, Honda, Ingredion, Lafarge Holcim, Michelin and Whirlpool.
“We really enjoy coming to this conference,” said J.R. Nield of J.R. Simplot. “It gives me the opportunity to bring my frontline guys to get them some education and some good training so that they can get their feet on the ground with oil analysis, proper techniques and the things we do onsite to save us money. There are numerous classes on different days and always something to learn no matter what level you are.”
Case Studies and Learning Sessions
Nearly 100 learning sessions on a variety of topics were available for attendees to choose from, including how reliability drives the bottom line, getting the most out of your maintenance efforts, best ways to predict and monitor system availability, and a complete guide to root cause analysis.
Case-study presentations were given by a number of prominent end users, such as Nissan’s Mark Beatty, who detailed how the Nissan North America plant in Smyrna, Tennessee, continued its journey to lubrication excellence after winning the John R. Battle Award from the International Council for Machinery Lubrication (ICML). Attendees learned how the plant was able to sustain its lubrication program, obtain management and employee buy-in, reduce downtime and save money, as well as how these same steps could be used to achieve results in any organization.
In their session, John Sexton and Douglas Bowker of BASF discussed how to use key performance indicators (KPIs) to manage and improve a reliability program. They also offered real-world examples of a reliability dashboard and took the audience step by step through each part to show how it was developed, how it is used and what value it can add.
Weyerhaeuser’s Christopher Brokopp presented an intriguing case study on how to change a lubrication culture. The importance of proper lubrication fundamentals and the right lubricant quantities were addressed along with advice for utilizing technologies such as ultrasound and vibration.
Paul Kimble and Jeremy Jeffers from the General Motors metal stamping plant in Marion, Indiana, described how their facility was able to develop an online vibration program for monitoring its stamping presses, which has resulted in detecting numerous anomalies and saving hundreds of hours of downtime. Attendees heard how the plant went from trying to collect vibration data once a month with a handheld data collector to collecting data every hour, 24 hours a day, seven days a week and 365 days a year while monitoring more than 1,000 points.
Michael Macsisak explained how Nestle Purina was able to successfully implement predictive maintenance (PdM) at its plant in Allentown, Pennsylvania, including how the organization developed its PdM program and kept it moving forward, which PdM tools were the most effective, and how PdM helped the plant add to its bottom line.
Ford Motor Company’s Gordon Van Dusen and William Harmych revealed how Ford performs root cause analysis for its equipment failures using a team approach. A step-by-step process of conducting a root cause analysis and the importance of communicating your findings were shared as well as advice for selecting the right team for performing the analysis, identifying the root cause rather than the symptom and the advantages of integrating the analysis into a maintenance data system.
“I attended every session I could, and they were all good,” said Elvis Reid, maintenance supervisor at the Saint-Gobain Abrasives plant in Brownsville, Texas. “It was all new information to me. The most beneficial part for me was just learning about how to clean hydraulic oil and how important it is. We are going to start analyzing our hydraulic oil in our presses and cleaning the oil, and I think I now have enough information to get the ball rolling. I got a lot of contacts.”
New Technologies, Products and Solutions in the Exhibit Hall
The exhibit hall featured 120 industry-leading companies and organizations showcasing a broad range of services and solutions. Many innovative products were also unveiled at the event, including new offerings from Luneta, Y2K Fluid Power, Pall Corp., Whitmore, TestOil, Generation Systems, SPM Instruments and MP Filtri.
“The exhibit hall brings to light the newest and most updated equipment, processes and applications,” said Michelin’s Steve Watkins. “For our plant and our reliability team, we actually take a lot of the information from all the vendors and bring it all together. That then gives us an opportunity to make a very wise decision on how we maintain our equipment.”
Reliable Plant attendees also were granted access to the exhibit floor of the Precision Machining Technology Show (PMTS). This international gathering of manufacturing professionals included more than 280 exhibitors displaying equipment, products and services to more than 6,000 attendees.
Opening General Session and Keynote
In the opening general session, veteran NASA astronaut Dr. Tom Jones gave a stellar keynote address on teamwork and leadership lessons from the astronaut corps. Having spent more than 11 years with NASA, flying on four space-shuttle missions, and working and living in space for 53 days, Dr. Jones recounted the good and the bad from NASA’s half-century-long experience in human spaceflight, from the terrible loss of the Apollo 1 crew and the triumph of the first moon landing less than three years later to the daring repair of the Hubble telescope and the preventable losses of two space-shuttle orbiters and crews.
“Excellent teamwork with no acceptance of substandard operations, preparation or execution was the concept upon which NASA built itself and all of its successes over the last 50-60 years,” Jones told attendees. “I’ve been able to see the product of that teamwork through my own missions into space. If you are going to be a leader in space and execute the right stuff, you have to trust and respect your team, show confidence that your team will perform, motivate your team toward a common goal and encourage teamwork. If you’re a lone operator in space, you are going to be either dead or a failure. You’ve got to be a member of the team.”
Attendees even had the opportunity to meet Dr. Jones and have him autograph two of his space and aviation books in the exhibit hall immediately following the keynote address.
Also during the opening general session, ICML presented the John R. Battle Award for lubrication excellence to Simmons Feed Ingredients along with the Augustus H. Gill Award for excellence in oil analysis to Newcrest Mining. Simmons was represented by several team members from the company’s facility in Southwest City, Missouri, including maintenance manager Tim Newman. Later in the week, Newman joined with Noria’s Seth Schroeder for a presentation on how the plant was able to reduce equipment breakdowns by more than 50 percent and achieve an annual cost savings of nearly $1 million once a greater emphasis was placed on lubrication.
Newcrest Mining’s Greg Romer was on hand to accept the Gill award and gave an interesting presentation detailing his organization’s award-winning approach for lubrication program management, including key targets and goals, the benefits of lubrication training, and using oil analysis metrics.
New for 2017
Four new certificate programs were added to Reliable Plant 2017, allowing attendees to increase their knowledge in condition monitoring, reliability engineering, hydraulics, and maintenance planning and scheduling.
Noria’s Jerry Putt launched the reliability engineering program with his pre-conference workshop on designing and procuring equipment to increase reliability. This informative workshop provided suggestions for designers and procurement professionals to achieve higher potential reliability and give their maintenance team a better opportunity to consistently realize optimum equipment capability.
The hydraulics certificate program began with a workshop from Chris Dellinger of GPM Hydraulic Consulting, who outlined five things you need to know to become an effective hydraulic troubleshooter. Dellinger described how to read and use a hydraulic schematic, proper pressure setting procedures, how to adjust a machine and troubleshoot individual components without removing them from the machine, as well as the correct reliability checks to make on the heart of the machine - the hydraulic power unit (HPU).
Doc Palmer of Richard Palmer & Associates Inc. opened the maintenance planning and scheduling certificate program with his workshop on how to achieve maintenance planning excellence. The author of McGraw-Hill’s Maintenance Planning and Scheduling Handbook, Palmer not only covered theories and principles but the nuts and bolts of how planning and scheduling work to help those in attendance implement a new planning organization or dramatically improve an existing one.
The condition monitoring certificate program drew the most interest and was led by Allied Reliability’s Walter Barringer, who described in his pre-conference workshop how to integrate multiple condition monitoring technologies for maximum reliability. This presentation explained how each of the four primary technologies works, when and where to apply each technology, which technologies to start with first in a new condition monitoring program, and how to choose equipment for inclusion in the program.
After the pre-conference workshops, certificate program participants were required to attend four key sessions over the next two days and then were honored at an exclusive champagne reception, where they received a commemorative plaque, a certificate of completion and a collection of books from the Noria bookstore.
Also new in 2017 were the six hands-on mini-workshops. These presentations gave attendees the chance to see firsthand some of the most important tools, procedures and equipment used in the field of lubrication and lubricant analysis. Noria’s Wes Cash and Loren Green demonstrated the steps for performing an effective patch test, taking a representative oil sample, reading an oil analysis report, maintaining a proper lubrication system, and keeping lubricants clean, cool and dry. Rich Wurzbach of MRG Labs also revealed how to determine if two greases are compatible and offered examples of grease compatibility testing.
A second keynote address was provided by Noria CEO Jim Fitch on why inspection 2.0 is your best strategy for detecting machine faults. Fitch explained how Inspection 2.0 seeks to penetrate and extract information from what’s been referred to as machine sign language, as well as how to translate this sign language into prescribed activities and instructions that stabilize reliability.
“Mission-intensive Inspection 2.0 is by far your most effective machinery condition monitoring strategy,” Fitch stated. “It’s hard for a machine to fail without the lubricant knowing about it first.”
Following the second keynote was a unique panel discussion on making the journey to reliability. Among the industry experts participating in the discussion included General Motors’ Kevin Grider, Kimberly-Clark’s Jeffrey Ng, Schwan’s Food Company’s Joe Anderson and Cargill’s Ted Melencheck.
The non-denominational prayer breakfast sponsored by SDMyers on Wednesday morning was highlighted by a keynote address from Ohio State University wrestling coach Tom Ryan, who gave his inspiring testimony while attendees enjoyed a hot buffet breakfast.
“Character is the foundational piece for sustained success,” Ryan explained. “You can see it all across the country and all around the world. When character is lacking, organizations fail and families break up. It’s this component of your willingness to chase the things you should and run from the things you should avoid. Talent and hard work will get us to the top, but only character and great decision-making will keep us there.”
Later on Wednesday, Reliable Plant attendees were offered a private guided tour of the Honda Heritage Center in nearby Marysville, Ohio, where they viewed historical, current and future Honda products, including innovative engines, race cars, motorcycles, jets and robotics. Guests were also treated to a special dinner and a commemorative gift.
The Tuesday and Wednesday evening receptions were the social highlights of the week and provided attendees with the opportunity to network with their peers while enjoying an assortment of hors d’oeuvres, drinks and entertainment.
A roundtable discussion on how to solve the most challenging plant problems enabled conference delegates to bring their toughest issues and receive coaching, problem-solving advice and a customized plan of attack for implementing all the great ideas and solutions learned at Reliable Plant.
In addition to the four pre-conference workshops, a post-conference workshop on lubrication excellence essentials for leaders was presented immediately following the three-day event. Onsite certification testing was also available from ICML and the Society of Maintenance and Reliability Professionals.
Show-prize Giveaway
Reliable Plant 2017 concluded in the exhibit hall with a special drawing for the show-prize giveaway. All registered attendees who visited each of the sponsoring exhibitors’ booths were eligible to win a Sea-Doo Spark watercraft. The lucky winner was Advanced Composites’ Charles (Chuck) Riddle.
“I can’t believe it,” Riddle said after his big win. “Honestly, I thought it was my partner when it was announced that the winner was from Sidney, Ohio, and Advanced Composites. I thought he won and not me. It’s indescribable. I didn’t think I even had a chance of winning to be honest. I’ve always won small stuff, like a tool here or maybe a $50 gift card, but nothing this big. It just blows your mind.”
Although he lives near two large Ohio lakes, Riddle acknowledged that he may end up riding his new Spark along Florida’s Gulf Coast where his girlfriend resides. He’s no stranger to this type of watercraft, as he has ridden his brother’s jet ski many times in the past. His company also makes the plastics that are often used on these types of vehicles. In fact, some of the plastic on the winning watercraft may have come from his company’s facility.
“We make plastics for all the automotive industry, some four-wheelers and jet skis,” Riddle explained. “We strew all the raw material, making the plastic pellets, and then send it to injection-molding companies where they form it into molds.”
2017 Proceedings, 2018 Registration Now Available
Even if you were unable to attend Reliable Plant 2017, you can still get the conference proceedings and benefit from the wealth of knowledge shared by speakers at the event. The new digital proceedings include the papers and presentations in PDF format from nearly every learning session. For the full 2017 conference proceedings, visit store.noria.com.
“I’ve had a great experience at this conference,” added Weyerhaeuser’s Christopher Brokopp. “I look forward to bringing some of the information I’ve learned here back to our mill and improving our lubrication. The availability of all the different technologies that are here is just great. It’s a great opportunity to learn easy things you can do to get that low-hanging fruit and improve your programs.”
Preparations are already underway for next year’s Reliable Plant Conference & Exhibition, scheduled for April 17-19, 2018, in Indianapolis. New case studies, learning sessions, certificate programs, workshops and an exhibit hall full of the latest technologies will be showcased once again. Registration is now open for Reliable Plant 2018, so don’t miss your chance to take advantage of the bottom-line results that attending this event has to offer. Visit Conference.ReliablePlant.com to register your team today.
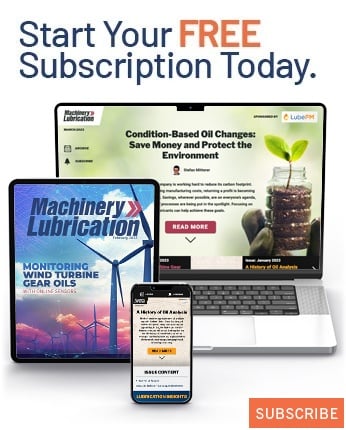