“How can you be proactive with your maintenance practices when you are currently in a reactive environment?”
Proactive change is never easy. Or is it? Maintenance departments that employ reactive practices are under the impression that this is the easiest approach. After all, with reactive maintenance little attention is needed until a catastrophic failure occurs. Then, everyone scrambles to correct the issues as soon as possible, even if it means overtime hours and extensive repair costs. Production is also likely halted in the meantime. Is this really the easier approach?
Those who have transitioned to proactive maintenance have realized that not only are there significant financial benefits from reduced equipment failures and downtime but that daily maintenance activities also become much easier.
While it may be simpler to determine how reactive maintenance should be performed, it eventually becomes costlier and more labor-intensive. On the other hand, it can be more difficult to decide how proactive or predictive maintenance should be executed, but it will be much easier and more cost-effective. Keep in mind that the longer a maintenance culture has gone down the wrong path, the harder it is to change those habits.
Below are a handful of practical suggestions to help transition from a reactive maintenance culture to proactive and predictive practices:
Enable Machines for Routine Inspections
This could be as simple as installing an ergonomic sight glass that allows anyone and everyone who walks by the machine to determine whether the oil level is correct and if the oil quality is good.
Control Ingression of Contamination
Install desiccant breathers on breather ports to prevent moisture and solid contamination in the environment from entering the machine.
Train for Knowledge and Motivation
Training can teach maintenance staff about the impact of contamination, lubricant selection and careful practices. This not only informs them of what to do but also motivates them to make a change because they now understand why.
Implement Oil Analysis
Oil analysis can be implemented through inexpensive field tests, such as viscosity comparators and blotter spot tests, or by utilizing a commercial laboratory for analysis with standard test slates.
Get Quick Wins and Show the Results
Focus on a small set of machines that have experienced issues in the past as a result of reactive maintenance. Implement proactive and predictive practices for some quick wins and display the results for everyone to see. This can help in the transition by providing an opportunity to reinforce the value of making the change.
Arguably the most important ingredient to evolve a culture from reactive to proactive maintenance practices is a change agent. This involves someone with leadership skills and credibility to plan and lead the change efforts within the maintenance team. This person must acquire the knowledge of what needs to be changed as well as disseminate this knowledge to the team carefully and repetitively. By following these suggestions, you can increase the chances of long-lasting results and a new, sustainable status quo.
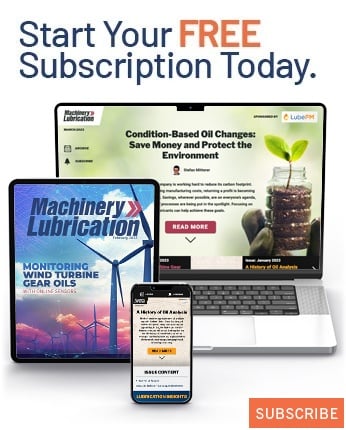