"Our organization once had a world-class lubrication program, but through many years and several personnel changes, we’ve seen our program decline to its current state of poor practices, contaminated oil, equipment failures and downtime. We’re now re-introducing the original plan for improving our lubrication methods, but do you have any suggestions for sustaining an effective lube program once that level has been achieved?"
With the baby boomer generation reaching retirement age and fewer skilled craftspeople to take their place, turnover and sustainability in many programs are becoming real problems. In years past, there was a natural process of technicians retiring and new hires being brought in to learn in an apprentice-style training mechanism.
This prevented the full staff from having to be replaced while also passing down the habits and practices that had been engrained into the organization, both good and bad. Today, it is not uncommon to have a complete personnel change every five to 10 years, which makes it more difficult to ensure that good practices are being taught and maintained in the plant.
If you haven’t already done so, the first step for sustainability is to document all tasks and processes. This provides a starting place for each new hire to learn what is expected and performed at the facility. Documentation can also serve as an auditing tool if there is any doubt that processes are not being followed.
These documents should be reviewed annually to make sure they are accurate and conform with industry best practices.
More organizations are moving toward a formal onboarding process for new hires that incorporates training for awareness and best practices. This type of training should cover specific practices that are unique to your facility. While much of the training can be completed online, field training should be included as well.
This may involve shadowing senior employees or having a dedicated trainer for specific tasks. There should be goals associated with the training along with an assessment at the end to evaluate comprehension and skill. The assessment should be geared to test both the knowledge of new hires and their ability to perform the task on which they were trained.
Simply receiving training at the beginning of the hiring process is not enough. Craftspeople should continue their education to stay current with industry best practices. Although many training courses are available, industry conferences also work well.
Just as with the training during the onboarding process, goals should be established for the event. Having those who attend the training give a brief presentation to their colleagues about what they learned can make the training stick.
Of course, policies and procedures will only get you part of the way on your journey. The element that makes the biggest impact in a program’s sustainability is having an internal champion who owns and is accountable for the program’s success. The champion doesn’t always have to be the team’s highest-ranking member but could be the one who is most influential in the group.
Getting this individual to buy into the program will make sustainability much easier. While there is no magic solution for enabling a program to withstand turnover, these strategies can help you build a solid foundation.
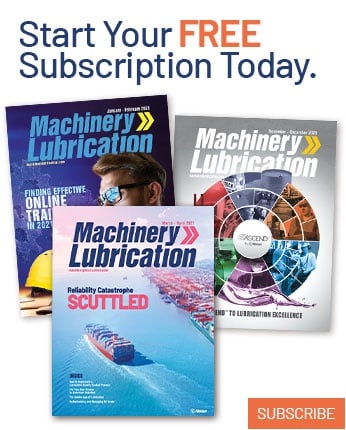