Lubrication is the cornerstone of any reliability program, yet few truly understand what all lubrication entails. It doesn't have to be a foreign language to you. Learn the basics of lubrication and the key terms that will further your understanding and ability to help drive your program to success.
Functions
Lubricants must be able to protect machine surfaces from degradation. They can do this in a number of ways. First, they reduce friction and, by doing so, help control wear. Lubricants also control corrosion, temperature and contaminants, which lessens the destruction of machine parts. Finally, they transmit power throughout the system. This is very common in hydraulic systems.
For lubricants to protect machine surfaces, they will be relied upon to separate machine parts with a film. This film could be a boundary film, which is formed by additives in the lubricant, or a fluid film, which is formed by the lubricant itself. The formation of these films is critical to the equipment’s longevity, as the films prevent excess friction and wear due to surface contact.
Boundary films are used during starts and stops, and depend on the surfaces being coated with an additive layer. These films can be made with either solid or chemical additives. Solid additives such as molybdenum disulfide and graphite adhere to mating surfaces to reduce friction and wear. They are more commonly found in greases.
Chemical additives such as zinc dialkyldithiophosphate (ZDDP) anchor themselves on the surfaces and are often found in oils. They provide a cushion for machine parts and help prolong their life.
A fluid film is when the oil physically separates the machine surfaces. These are classified into hydrodynamic films, which occur in sliding contacts, and elastohydrodynamic films, which are found in rolling contacts. The main contributors to this phenomenon are speed, load, temperature and viscosity of the fluid.
Viscosity can be thought of as the oil’s thickness. It is the most important physical property of a lubricant. If the viscosity is too low, you will not be able to generate these films. If it is too high, there will be excess drag and fluid friction in the system.
Contamination
Perhaps the most avoidable issue associated with the use of lubricants is contamination. Contaminants can enter a lubricant throughout its life cycle but are most common during the handling stage when the lubricant is exposed to the atmosphere and contaminated tools.
Employing best-practice top-up containers and filtration for all oil will have a dramatic impact on the number of contaminants and the life of both the oil and equipment.
When the lubricant is in storage, ideally it should be in a dedicated lube room that is climate-controlled, access-restricted, centrally located and sized appropriately to store all items in the program. The use of storage lockers allows for the organization of all hardware and miscellaneous items.
For oils that are used more extensively, a dispensing unit equipped with filtration devices dedicated to each individual lubricant is recommended for most applications.
Labeling all items associated with the lubrication program is a great way to reduce cross-contamination and ensure the proper lubricant is applied in the field. Tags should be affixed to the machine, top-up container, filter carts, dispensing system or anything that may contain oil or grease. To avoid confusion, these lube tags should be color-coded with a shape and code that are unique to a particular lubricant.
Lubrication doesn’t have to be complicated. A good lubrication program can be built on a few key concepts. Keep all lubricants clean, cool and dry; select the proper lubricant for the application; and label everything to avoid cross-contamination. While these steps can be accomplished in a number of ways, they must be in place for any lubrication program to succeed.
This article was previously published in the 2018 Machinery Lubrication Conference Proceedings.
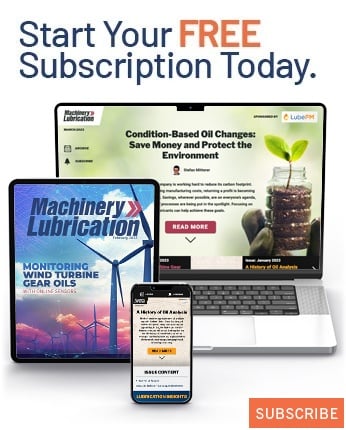