In working with maintenance and reliability teams across different industries, Noria has noticed that the lubrication costs allocated in a typical budget often do not seem as significant as other maintenance and operational costs such as parts and labor. Consequently, lubrication is regarded as a lesser function. This perception is worsened when lubrication is viewed as a dirty job.
However, what frequently is not taken into account is the cost of dated or incorrect maintenance practices. Many high-level leaders are not aware of the impact these unnecessary costs can have on their plant budget or of the benefits that can be realized by implementing an optimized reliability strategy, of which lubrication is a critical element.
During Noria’s public training courses, engineers and technicians have often said how they would like their managers to attend these seminars to understand the opportunities for improvement and savings in their facilities.
Upper management generally deals with financial numbers, and almost everything in the organization is seen from a financial perspective. Wouldn’t it be great to show the plant manager, chief financial officer and company president the tremendous opportunities they have to invest in plant reliability while realizing a high return on investment by reducing operational costs?
How can you make them aware of reliability concepts and principles so they can convert them into numbers? This article will help you reveal the hidden costs so they can be better understood from a business perspective.
Hidden, Unnecessary Costs
What are the hidden costs? It’s possible to measure or estimate them if resources have been provided for training on failure modes and investigations, as well as a methodology and resources to conduct failure investigations. Also, a computerized maintenance management system (CMMS) can record and keep detailed information on the conclusions from failure investigations, machine/fleet failure frequencies and modes, relevant issues about equipment operation, and estimates of the cost per machine failure and failure modes for the fleet.
While this information can be helpful, it is quite difficult to reach this point. Frequently, there are no resources or methodology to collect, process or analyze the information. There may also be failure root causes of which the maintenance team is unaware. In addition, the root causes can be combined, and it may not be possible to identify all of them or determine their relevance. A few estimates of hidden costs are shown in the illustration below.
How can the cost of lubrication-related failures be so much higher than what is seen in the accounting system? The answer is there are diverse failures that may not be catastrophic but that produce diminished performance of the machine components, which makes it necessary to schedule a repair or replacement. In many cases, the failure is silent and relatively slow, so it is not perceived as an abnormal condition but rather a normal machine operation or part of the typical equipment life cycle.
Although this principle is applicable to nearly all machines, one component that is particularly susceptible to lubrication failures is the rolling-element bearing. The replacement cost for bearings can be five to seven times the cost of the actual bearing due to labor, administration, warehouse stock control, purchasing procedures, etc. These direct and indirect costs may go beyond the limits of the maintenance budget.
Following are a few industry examples that demonstrate this type of silent, unperceived wear which at the end of the day must be paid by the maintenance and operations department.
A Satisfied Culture
Some companies are so financially healthy that the old or traditional maintenance strategies are accepted. In these organizations, it is important to have machines working as much as possible to maintain production. Typically, few people in the company will be interested in optimizing resources, since it seems like an unnecessary strategy and there is no perceived need for improvement. Eventually, this culture of being satisfied with the current condition will reach all organizational levels, from top management to floor personnel.
On the other hand, some companies have been through tough times and realize the importance of optimizing costs and looking for better productivity with fewer resources. These organizations are more open to talk about reliability and reliability-centered lubrication.
Preventive Maintenance Masks Corrective Maintenance
When the maintenance team for a continuous-process company that operates 24 hours a day, seven days a week reported no serious issues with bearing failures and that the plant was working well within the scheduled shutdowns, it was both surprising and somewhat concerning. When the plant’s lubrication and contamination control practices were analyzed, gaps in the design and execution of the routines were identified as well as significant sources of contamination during the storage, handling and application of oils and greases.
Most of the preventive maintenance was not actually inspections, lubrication tasks, replacement of consumables, etc., but rather corrective maintenance that was scheduled every six months. The team had been replacing numerous bearings in the scheduled shutdowns and were satisfied with this situation because they rarely had unforeseen downtime due to bearing failures. So, while the cost of unexpected production loss was low, the maintenance costs were high.
A similar conclusion was reached at a wastewater treatment plant where a large, plain bearing for a mixer was replaced every two years. This was accepted as normal until someone further investigated the correct lubricant for the component. When the grease was upgraded, the bearing life was extended to more than 10 years.
No Budget for New Projects
I recently met with a maintenance team and a plant manager at a large facility to discuss their opportunities for cost reduction and investments in a reliability strategy. Someone remarked that the benefits were obvious but the concern was obtaining corporate approval for the required technology, training, new lube room and lubrication procedures. The current budget also was already allocated for other purposes.
A few questions were then asked. How much money was already invested in components and spare parts that were waiting in the warehouse to be used when something failed? The answer was probably several millions. Also, how many bearings were replaced across the plant over the last 12 months? The answer was several hundred.
You may be wondering how it’s possible to have money to fix equipment issues while at the same time dealing with a restricted budget for investing in the elimination of the root causes. When there is inertia with corrective practices, it’s like a snowball that cannot be quickly stopped. That’s why it is essential to allocate your budget and human resources to drive the change.
Failure Rates Are Already Low
A phenomenon some industries often cope with might be termed “waves of reliability.” This is when someone proposes implementing a better reliability strategy while failures are frequent and corrective maintenance is the norm. A more stable maintenance deployment plan is put into place.
Changes occur, and positive results are seen. Then, after a few years, when there is pressure to lower costs or new management is brought in, the successful reliability practices are reduced or eliminated, returning the facility to its previous state and increasing the number of failures.
Keep in mind that properly installed, operated and maintained machines generally have a long life, regardless of the industry or machine type. If you experience repairs or replacements within a relatively short period of time (a few months or one to two years), you likely have the potential for improved machine reliability.
Oil Analysis Program Has Become Routine
Over the years, Noria has seen many instances when the oil analysis program for a plant or fleet has become routine. Oil samples are taken and sent to the laboratory. When reports are received from the lab, they are quickly scanned for any flagged issues. If an abnormal condition is detected, action is taken, such as an oil change.
However, when the program’s effectiveness is studied in depth, it often is discovered that some of the red and green flags were not accurate, certain samples may not have been collected properly or results were not interpreted according to the machine’s specific conditions. Also, statistical analysis of the results may not have been performed to identify failure patterns or the need for maintenance improvement.
In addition, if personnel do not have an understanding of oil analysis or have not had specialized training, they may be unable to detect errors or know that other tests can be used to analyze the oil. Remember, oil analysis is a powerful resource with diverse technologies and should evolve with your reliability program.
Areas to address when creating a case study
Discovering the Value of a Reliability-centered Lubrication Program
A reliability-centered program is focused on improving machine availability while ensuring that the equipment is working at full capacity. It is a combination of machine availability and productivity. This combination reduces unnecessary maintenance and operational costs.
A good example of the value that can be gained from a reliability-centered lubrication program recently occurred at a facility that manufactures construction materials. When a lubrication benchmark assessment was conducted about five years ago, the results were poor, and there were many opportunities to implement better practices.
Top management decided to support an improvement project. After three years, they requested a new benchmark assessment. The results were much better. A lubrication technician then offered his testimony. He explained that his job title of “lube tech” had remained the same, but his role had changed. Three years earlier, he would take a deep breath before entering the plant each day, as he prepared for the problems and stress that would be experienced that day, including oil changes, leaks, lubricating repaired or replaced machines, etc. Three years later, his job had changed significantly.
The level of stress had been reduced, and his duties were more related to checking and maintaining lubricant cleanliness, keeping the lube room in good condition, working on the scheduled lubrication and inspection plans, etc. Management also reported that it would be able to cut 20 percent of the total mechanical maintenance budget, which represented a competitive advantage in terms of operational costs.
Creating Your Own Case Study
How can you create a case study that demonstrates better results? Specific steps should be taken that follow a methodological approach. First, identify where your facility or fleet is in terms of implementing best practices. A benchmark assessment can offer valuable information on the practices and controls for the entire lubricant cycle, which includes selection, reception and storage, handling and application, analysis and disposal.
Both the assessment and goals of lubrication excellence (see sidebar below) can provide good ideas for where to start your case study. The improvement plan should include well-defined targets and milestones supported by the necessary resources to achieve the goal in a reasonable amount of time.
Also, define key performance indicators (KPIs) to monitor the project. This is not always easy, since effective indicators require information about quality, consistency and availability. The indicators should measure examples of inefficiencies that are expected to be controlled with the project. Expectations should not be set too high in the short term, as some time will be needed for the numbers to progress.
Finally, consider the story of a bauxite mine that was facing difficult times due to frequent shutdowns and high maintenance costs. After four years of working to implement a reliability strategy with lubrication excellence as the primary component, the plant documented a substantial payback. An investment of $1 million resulted in a return of $5 million at the completion of the project. Keep these achievements in mind as you create your own business case study, and don’t forget that success is possible.
Lubrication Excellence Goals
The goals of lubrication excellence can be defined as:
-
The four rights: right lubricant, right amount, right frequency and right lubricated component
-
Keep the lubricant contaminants controlled: clean, cool and dry (no excess temperature).
-
Do it consistently. Regardless of who is executing the job, it must be done following the same best practices. This requires training, procedures, tools, communication and team alignment.
-
Follow best practices according to machine criticality, operational conditions and risk.
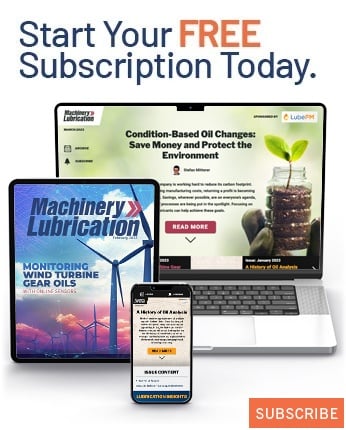