Contamination control is one of the most important strategies for keeping lubricants performing optimally. A lubricant will last exponentially longer if it is kept clean, cool and dry. The first step in contamination control is to identify which contaminants pose the greatest risk. Solid particles, water and air are the most common contaminants.
Solid contaminants include dirt, metal from internal machine wear and debris. Other concerns may involve glycol contamination, which can cause oil thickening and wear, along with fuel, which can accelerate oxidation and lead to thinning of the lubricant film. Depending on the application, radiation can also be a contaminant.
After determining the possible contaminants, you must then consider their effects on the lubricant. These effects can vary depending on the contaminant, its concentration or severity and the lubricant’s application. For example, particle contamination can result in the mechanical destruction of machine surfaces, such as abrasion and surface fatigue (pitting).
Air contamination may cause oil compressibility, film strength failure, cavitation and varnishing. Water contamination can affect the lubricant’s additives as well as the machine. In the base oil, moisture can lead to oxidation and hydrolysis, thus changing the lubricant’s chemistry. This can promote varnish, a change in viscosity and acid formation, which can severely impact the life of the machine.
Fortunately, contaminants are controllable through exclusion and removal methods. Exclusion refers to all actions that will prevent and keep contaminants away from the machine, while removal focuses on the elimination of contaminants that currently exist in the oil inside the machine.
Keep in mind that new oil does not mean clean oil. Always ensure that your new oil is filtered before it is used. Once the lubricant is in use, employ proper breathers and headspace management techniques to protect the lubricant from water, air and solid contaminants as much as possible. Filter carts also provide a great way to keep oil clean and performing at its best. These carts can be utilized to clean stored lubricants, for off-line filtration and even for flushing the machines.
Remember, contamination control is just as important as choosing the proper lubricant for the application. After all, it would be pointless to spend lots of money on the best lubricant if more must be spent to replace it because it has been contaminated or ruined. Be proactive with your contamination control efforts, so it won’t be necessary to replace the lubricant or, even worse, the machine due to wear.
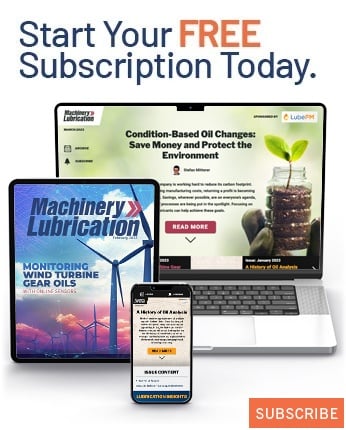