When most people think about safety, they usually consider their personal responsibility for staying safe. At any plant I visit, safety typically is among the first topics discussed, and it’s almost always targeted toward what individual actions must be performed.
This includes which personal protective equipment (PPE) to wear, what areas to avoid, which sirens or alarms to be aware of, what the fire or severe weather plan is and other related items. Many sites even have employees and contractors wear a visible sticker or badge that shows a proper safety briefing has been completed.
However, when it comes to the specific tasks associated with a lubrication program, the general safety training and knowledge in most plants is insufficient. Safety should be the top priority on a jobsite, and the lubrication program’s design should be part of this safety prioritization.
When establishing a culture of safety around your lube program, there are six main elements to consider: general safety, training, storage, handling, worksite monitoring and disposal.
General Safety
Work within the existing safety programs at your site. Take advantage of the rules and regulations currently being enforced and decide how they apply to lubrication practices. Your company has already committed to employee safety and well-being, and determining how your actions fit into these existing practices will go a long way toward your success.
For example, many oil sampling or fill points can be in hard-to-reach locations. Guidelines likely are in place for how to properly gain access to those spots, such as fall protection for working aloft or how to position a ladder to reach over a run of piping. Incorporate the current safety framework at your jobsite, from PPE to cleanliness and anything else the health, safety and environment (HSE) team has set in place to ensure overall company safety.
You should also work with your HSE team to contribute lubrication knowledge to existing safety standards. Help them identify hazards and assess risks in specific lubrication matters.
Lubrication is used to help equipment move, and by definition, moving equipment is dangerous. Perform a comprehensive survey to examine hazards in the workplace, such as the work area layout, as well as activity hazards like the specific machinery being used and environmental hazards like combustible dust. Create written procedures for lubrication activities in the same way you would for other maintenance or HSE-related work.
Training
Train on safety regularly. Along with incorporating current HSE practices into your lubrication program, you also should train all personnel in the particulars of lubrication safety. For many, this will just be general awareness training and can be added to the annual queue of refresher training that the HSE team rotates through, similar to confined space or hearing conservation.
For those who are more actively involved in performing lubrication actions, a more robust safety training will be needed. Specific knowledge of the location and identification of lubricants using the safety data sheet (SDS) program will be vital. Consider including hands-on training sessions for sampling and drain/fill evolutions.
Some good rules of thumb for when to provide training would be for first-hire employees (general safety and job specific as needed), when an employee is changing positions or responsibilities to include more lubrication, or when a change or implementation in processes is being made, such as a new lubrication type being added, a new piece of lubrication equipment being used, or some other hazard or condition being introduced. Refresher training should also be offered based on the company or group need or by regulation (at least annually).
Storage
As the old adage states, an ounce of prevention is worth a pound of cure. Properly storing and containing oils and greases will go a long way toward making your lubrication program safe. There is no single right way to store lubricants safely, but there are many wrong practices for managing lubricant storage. Common factors that contribute to stored lubricants being unsafe are as simple as weather exposure or storing lubricants in high-traffic areas. Precipitation and direct sunlight can corrode barrels and other metal connections. Corrosion may result in leaks or escaping fumes from barrels or other storage totes.
Exposure to the environment can also damage the lubricants. Damaged oil being pumped through your systems can lead to earlier machine failure and possibly catastrophic failure, which is far more alarming for most workers than spotting a sheen of oil heading to the environmental drains.
Design your lubricant storage to help prevent spills or leaks by keeping lubricants inside and away from high-traffic areas or pipes that are known to leak or vent, such as steam traps. Store tools and smaller lubricants like greases in specially designed lockers to prevent fire or contamination. Additional ventilation or atmospheric monitoring may be needed to meet air-quality regulations.
Follow all guidelines established by the Environmental Protection Agency (EPA) and Occupational Safety and Health Administration (OSHA) concerning the storage of lubricants, including oil breaks, approved drains, stacking and positioning of containers, and fire suppression or ventilation systems. Work closely with your HSE team to ensure any changes to your lubrication program take these regulations into account.
In the illustration below, you can see many of these safe practices at work. The lights and electrical are rated as explosion-proof, a ventilation system has been installed in the ceiling, a fire-suppression system is employed, the floor is sealed to prevent seepage from leaks into the ground, and there’s a proper waste-disposal receptacle for rags and other rubbish.
An example of a proper lubricant storage room
Handling
While many lubricants are nontoxic, some may contain a trace mineral or ingredient that can cause a reaction or injury if mishandled. Read the SDS for the lubricant in question and keep copies readily available for workers who use the area.
Some common lubricant classification types are listed above with approximate toxicity concerns. Additionally, the American Petroleum Institute (API) has classified all lubricants into one of five groups with specific warnings. Group I lubricants have been identified as having sufficient evidence of carcinogenicity to humans.
The carcinogenetic component is called a polycyclic aromatic hydrocarbon (PAH), also referred to as an aromatic. If your facility handles Group I lubricants, be sure to take extra precautions, such as large placards or other warning signs to keep unknowledgeable team members away.
Similarly, Group II lubricants have been identified as having possible carcinogenicity to animals. While not as dangerous as Group I, these lubricants require the same types of precautions and warnings. Group III and IV lubricants have been treated in such a way as to remove most aromatic compounds, but some components may still be of concern.
Lastly, Group V lubricants are chemically engineered esters, polyglycols and silicone based. In this group, attention should be paid to any phosphate esters, as these compounds have the most potential to harm humans. Allergic reactions are also common for triphenyl-phosphate compounds.
Keep the appropriate PPE nearby, such as gloves, goggles, face shields or other safety gear. Practices that help to prevent spills, leaks or overuse should be employed, such as using a metered filter cart with quick disconnects for transferring or filling oils from storage. When sampling, use a pressure reducer if the oil is normally more than 100 pounds per square inch gauge (psig).
Greases have a few unique handling precautions as well. These lubricants tend to settle in the tube when stored at lower temperatures and may need to be warmed before applying. Grease shouldn’t be manually warmed above 75 degrees F and should never be warmed with any sort of flame. Also, never hold a grease gun coupler with your hand during application, and consider using grease guns with an installed pressure relief or avoiding pneumatic types for high-risk situations.
Worksite Monitoring
After any lubrication activity, such as draining, changeouts or filling, always recheck the worksite and equipment. Look for leaks or spills. It’s possible a seal or cap wasn’t properly reinstalled. Dust or debris may have settled on a small spot that wasn’t noticeable during the maintenance task and now presents a potential hazard.
You may wish to schedule monitored lubrication evolutions. Observe how the lubrication activity is planned and carried out by the maintenance or operations personnel who deal with it each day. This allows for process improvement and helps shore up weak areas of safety training and practices.
Include the lubricant storage area as part of any group cleaning of the plant to encourage personnel to become familiar with the equipment as well as how tools and lubricants should be used and stored. This not only serves to keep the area safe because equipment is properly maintained, but also ensures safety for other concerns like slips and trips.
Disposal
Used lubricants that are awaiting disposal are just as important to store properly as new oil, if not more so. Used oil may have contaminants or expired additives and present different chemical properties than new oil. Used lubricants often are mixed and may have different flash points than the base oil. Store used oil in a separate area from new oil and follow local HSE rules for combining different types of discarded oil or other products, such as oily rags.
For used filters, the best practice is to separate the metal portion for recycling, compress the media to remove the oil and dispose of the oil in a used-oil container. This reduces the fire risk from discarding the entire filter in the trash. Dispose of greasy or oily rags in proper disposal cans and don’t allow them to accumulate or become a hazard. When cleaning equipment, use approved solvents or soaps and ensure any runoff goes to an approved environmental drain.
In short, store your lubricants correctly, handle them well, dispose of them properly, double-check your jobsite, follow all site-specific safety guidelines, and train to the standard by which you want the program to live. In most companies and worksites, safety is priority one. Performing lubrication tasks should be no different. Deliberately adopt a safety-first mindset to plan, execute and evaluate all the lubrication efforts at your plant.
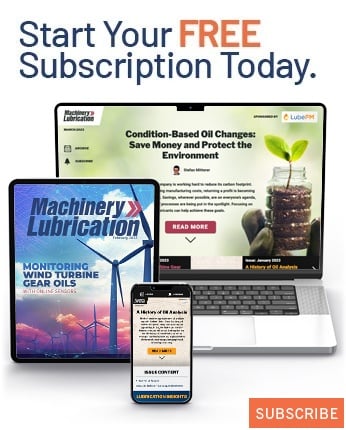