Everyone is performing or learning something at any given moment. Some skills we are good at, and others we are not. Yet just because we believe all is well with a particular skill doesn’t mean we couldn’t be better at it, but how would we ever know? This is where the four stages of competence come into play.
The four stages model provides a means to describe how people learn new skills. Developed roughly 50 years ago by management trainer Martin Broadwell and popularized by psychologist Noel Burch in the 1970s, this model is also known by other names, such as the four stages of learning, the conscious competence ladder, among others.
Most often, these stages are related to the learning journey of an individual, but could they be applied to a maintenance organization? In a nutshell, the four stages represent a progressive matrix of consciousness and competence:
Stage 1: Unconscious Incompetence
A person is blissfully unaware of his or her shortcomings in regard to a particular skill set. The length of time a person remains in this stage depends on how motivated he or she is to learn.
Stage 2: Conscious Incompetence
Once the person is made aware of his or her shortcomings through one or more resources, the person acknowledges that new skills will be necessary to resolve these deficiencies. Hopefully, the person starts to learn these skills.
Stage 3: Conscious Competence
The person practices these new skills, deliberately thinking through each step and procedure.
Stage 4: Unconscious Competence
The new skills become second nature or habitual, performed competently without any extra concentration or special effort.
Surely, these four stages apply individually to lubrication practitioners who go through the rigors of training and certification. Self-awareness allows people to know not only the stage at which they are currently with a particular skill, but also what they need to do next to get better.
When to Become Certified
It is an honest question: At which stage would we find candidates to be most receptive to training and certification? The answer might be open to friendly debate, but I would suggest that stage 2, conscious incompetence, is where most practical training begins. Although stage 4, unconscious competence, is where certification might make most sense, I would argue that certification is more impactful as a bridge from stage 2 to stage 3 as practitioners start to apply what they are learning.
Stage 1, meanwhile, is where you would find those who are not yet ready for training, because they innocently never consider the value or necessity of exposure to new ideas and information.
Applying the Model to a Plant Lubrication Program
Does this model hold up when applied within the context of a departmental lubrication program? Yes, but this scenario consists of individuals working together in concert, so an organization’s stage of competence can be gauged by the aggregate competence of its team members along with the efficacy of its lubrication program through which those team members perform their duties. Because of these conditions, the delineation of the four stages is not as clear, as they tend to overlap.
Regardless, you can see a common pattern across case studies, because even institutional learning starts with the status quo and advances on the strength of curiosity, the reception of good training and the application of “practice makes perfect.” Somewhere along the way, the professional certification of individuals, combined with recognition of a plant’s success story, can confirm newfound levels of competence.
Stage 1: Lubrication Status Quo - All is Well
At the unconscious incompetence stage, a maintenance organization may be working in its own bubble of key performance indicators (KPIs). Without external data that compares its lubrication performance and expenses to similar organizations or to industry standards, the department subjectively performs activities without knowing whether they are optimized.
Phrases associated with this stage might include, “If it ain’t broke, don’t fix it,” and “We are doing good: only three gearbox replacements this quarter!”
Such an organization likely comprises individuals who possess practical knowledge of such subjects as asset optimization, contamination mitigation, lubricant selection factors, best practices for lubricant storage, etc., but they do not necessarily apply this knowledge or even appreciate their own relevance to the larger scope of business objectives.
In this stage, organizational leaders dispute the benefits of comprehensive lubrication programs and professional certifications, because they naturally assume everything is already as it should be, without realizing things could be better. This is not a resistance to change for change’s sake. Rather, it stems from a lack of understanding of the value proposition that training and certification can offer to a lubrication program.
Stage 2: We Can Do That?
At the conscious incompetence stage, someone has presented the organization with evidence that there is tangible value in the formal development and sustained application of a lubrication program. This evidence comes from reading industry magazines, attending conferences and exchanging stories with other companies. Additionally, case studies are good tools to plant seeds of awareness that can shake people out of stage 1 inertia.
Such exposure is often the result of managerial mandates like, “read this magazine,” “take this online class,” or “attend this conference.” There is something to be said for forcing educational opportunities upon lubrication personnel. Managers who require continuing education are doing their teams a favor, helping ensure they do not remain stuck comfortably in stage 1 forever.
Stage 2 is where the term “low-hanging fruit” likely is introduced. Frequently, an internal audit of machinery assets, lubrication procedures and institutional knowledge is conducted at this stage to confirm the potential return on investment (ROI) of new actions that might be initiated.
Not all organizations that become aware of the possibility for improvement turn immediately to third-party consultants for guidance. However, all organizations that want to resolve their recently recognized lubrication deficiencies will start shopping around for training, certification, equipment, products and procedural solutions, regardless of how they eventually intend to manage their lubrication programs. Certifications are always third-party affairs.
Sustainability Is Purpose-driven
Because the pursuit of training can be a daunting task, stage 2 is where most lubrication programs die. This is why an organizational purpose (objectives, goals, etc.) is so important. Any team can increase its aggregate brain trust by sending its most receptive lubrication practitioners to formal training to ensure consistent expansion of institutional knowledge. Ideally, these individuals will train and learn so they can proceed to apply best practices in stage 3.
Of course, change is hard, but it can be made easier if the practitioners perceive a larger organizational purpose. This can be as simple as setting new KPIs to break old maintenance records or focusing on winning an industry award for the facility - anything measurable that helps an organization (and its individual members) to stay motivated and avoid feeling overwhelmed.
From a management perspective, it is essential to be careful when spending training and certification time and dollars to ensure gains are made in areas that are obvious and important to team members. After all, what is the point of increasing your department’s competence in areas that don’t align with organizational goals?
Stage 3: We Are Doing It!
In the conscious competence stage, the organization faces ongoing challenges spread across several months or years. Those who drive change to lubrication and oil analysis understand that success will require a new plan developed in accordance with the organizational purpose and objectives. This plan must be executed in such a way that creates opportunities for individual practitioners to focus as much as possible on honing their new skills. At an organizational level, it is not just skills that must be practiced but also new policies, procedures and priorities.
Change leaders in this stage understand that success requires compliance even outside the immediate lubrication program. Accordingly, they will encourage cross-departmental training and instruction so all stakeholders (especially at executive levels) recognize the potential value of new lubrication activities.
In stage 3, lubrication program development is focused and deliberate. One of the biggest challenges is breaking down departmental policies or habits in favor of new ones that provide more agility and machinery uptime. This is where you will hear talk about a culture change. Hands-on practitioners are engaged with managers to transform the organization’s program to world-class status. Hiring third-party consultants and earning certifications may or may not occur in this stage, but both would certainly accelerate progress through stage 3.
Stage 4: The New Normal
At the stage of unconscious competence, all stakeholder groups are on the same page with high expectations for maintaining new KPIs and new levels of machine reliability that meet business goals. All practitioners, managers and suppliers recognize the big-picture relevance of new lubrication and oil analysis activities. Old habits are no longer a source of friction. The organization understands there is no value in scaling back on any of the changes, because they have verified ROI (e.g., lower expenses, greater uptime, etc.).
Achieving stage 4 as an organization doesn’t mean that every part of the lubrication program comes effortlessly to every individual on the team. What it does mean is that institutional resistance to change has ceased and that organizational expectations and capabilities are naturally elevated. Checklists and formal procedures are still necessary to ensure consistency, especially as new hires go through their own individual stages of competence to get up to speed with the team.
Continuing education and certifications are common here, but such activities only occasionally cycle individuals - not entire organizations - back through the stages for specific aspects of the lubrication program. However, over time, the sustained presence of certified practitioners and managers mitigates erosion of an organization’s stage 4 competence.
Organizations in this stage set the curve for world-class competition. These are the plants that normally submit applications to the International Council for Machinery Lubrication (ICML) for the annual Gill and Battle awards. To read stories about successful lubrication and oil analysis programs, visit the ICML website at lubecouncil.org.
In Which Stage Is Your Program?
It is no simple undertaking to adopt and embrace lubrication and oil analysis improvements for your organization while simultaneously pursuing and earning professional certifications for yourself and your crew. If you are trying to develop a facility-wide lubrication program, it is important to determine where your colleagues are - and where your organization is - within the four stages of competence. As a leader, your job is to accelerate through the stages as quickly as possible so both your team and plant can soon become unconsciously competent and reap the benefits of lubrication excellence.
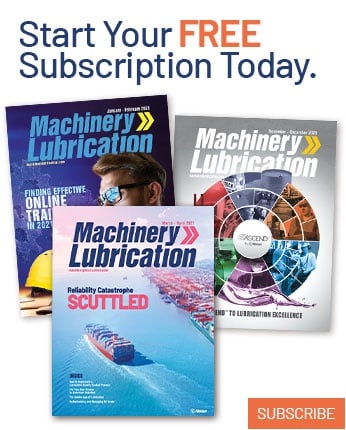