Oil mist is an aerosol mixture of one part oil to 200,000 parts air. It is generated by passing high-velocity air through an orifice that pulls oil into the air stream. The high-velocity air stream breaks the oil into particle sizes of 1 to 3 microns, thus the resemblance to cigarette smoke or steam.
The same air, at a much lower velocity and pressure, then transports these small oil particles through a distribution system to the equipment to be lubricated. These small particles are referred to as dry mist and are much too small for lubricating purposes; however, they are easily transported throughout distribution systems over distances of 600 feet.
For lubricating bearings or other equipment, dry mist is converted into wet mist prior to the equipment being lubricated. This is accomplished by passing the dry mist through a reclassifier (Figure 1). As these small particles pass through the reclassifier orifice, the increased turbulence causes the particles to stick together and grow in size. At this point, the oil mist is referred to as wet mist. The larger wet mist particles are now applied to bearing surfaces and can lubricate rolling-element bearings.
As wet mist is applied to the equipment with an air-flow velocity of 24 feet per second, this same air must also be vented from the bearing housing to allow the mist to move onto and across the bearings to provide lubrication.
The flow of oil mist into the bearing housing creates a slight positive pressure (above atmospheric pressure) inside the bearing housing, which prevents the intrusion of airborne contaminants. The flow of oil mist supplies continuous lubrication to the bearings and passes onto a vent point. The excess oil mist must be contained and collected below the equipment for reuse or disposal.
This method is an excellent means of lubrication for bearings with speeds of 500 to 3,600 revolutions per minute (rpm), and is preferred for bearings operating in the 10,000 to 15,000 rpm range where splash lubrication is ineffective. Oil mist is also considered best practice by the hydrocarbon processing industry and is recommended within the specifications of the American Petroleum Institute (API).
Figure 1. Oil mist reclassification
Verifying That Oil Is Reaching Each Bearing
The reclassifier, which controls the amount of lubricant being applied to each bearing, is sized using the same calculations for rotating equipment bearings. Reclassifiers can create back pressure throughout the mist feed lines. Plugging in the lines causes high pressure, while a broken line will result in low pressure. An oil mist generator monitors the pressure, using high- and low-pressure alarms, as well as the mist density for under- and overlubrication of the equipment.
Installation of the piping system should be closely monitored for cleanliness. Once the system has been installed, it should be blown with air for eight hours for additional cleaning. After startup, only one thing can plug the system’s reclassifiers - wax from paraffin-based oils.
The waxing problem is well known to most oil mist users. Synthetic lubricants or high-grade, wax-free mineral oils are commonly used in these systems. Should waxing occur, all the reclassifiers can become plugged within an hour, causing numerous alarms to sound in the control room. With modern-day oil mist systems, plugging of reclassifiers is a rare occurrence when quality lubricants are used.
Figure 2. The gas blower’s original oil console
(Ref. Hydrocarbon Processing Magazine)
Suitable Equipment for Oil Mist
Oil mist is recommended for most types of rolling-element bearings operating between 500 to 15,000 rpm. The most common applications are pumps and motors. Approximately 30,000 pumps in the U.S. refining industry are lubricated with pure oil mist, along with an equal number of motors.
Lubricants Used in Oil Mist Systems
A diester-based oil is preferred for oil mist systems but is not required. All major lubricant manufacturers have mineral and synthetic oils that can work well in these systems. An ISO viscosity-grade 100 oil is recommended for most systems except where temperatures commonly fall below 32 degrees F. In cold-climate systems that operate at temperatures below 32 degrees F for long periods of time, most users drop down to an ISO viscosity-grade 46 or 68 oil.
When selecting a lubricant, contact other oil mist users in the area to see which lubricants are being used and how they are performing. All oils are not equal. Most are blended for sump or splash lubrication. With oil mist, the oil is broken down into micron-sized particles, which may allow the additive package to fall out of suspension if the oil is not properly blended.
Be careful with mineral oils that have a paraffin base. Too much paraffin can plug the reclassifiers in the system during hot summer or cold winter temperatures. Therefore, always select paraffin-free oils and never use automotive oils in oil mist systems.
Figure 3. The upgraded lubrication system incorporating oil mist
(Ref. Hydrocarbon Processing Magazine)
Minimum/Maximum Operating Temperatures
Oil mist does not have a high or low operating temperature. However, oil mist generators will have a low ambient temperature of minus 40 degrees. For hot climates, air coolers are included in the units to prevent heat damage to the electronic components. After the oil mist is generated, it becomes the same temperature as the header pipe. The outside temperature has no effect on the oil mist particles that are in suspension within the piping system.
Pure oil mist is often used on process pumps that have temperatures of 600 to 750 degrees F. Rolling-element bearings seldom operate at temperatures higher than 200 degrees F.
Keep in mind that oil mist does not support combustion and is well below the limits for flammability. It also is below the Occupational Safety and Health Administration’s allowable limit of 5 milligrams per cubic meter of air for an 8-hour period. With a closed-loop system, the amount of oil in the air is far below the allowable limit.
System Reliability
Oil mist systems have no moving parts, so there is nothing to wear out. According to mechanical engineering expert Heinz Bloch, an oil mist generator is 99.99 percent reliable. The two requirements for the generation of oil mist are clean instrument air and clean oil. Electricity is not necessary for system operation.
In regard to the air supply, the maximum consumption is 30 standard cubic feet per minute (SCFM) for a large system that would serve 50 to 80 pieces of equipment. Should the air supply system go down, there likely would be many more issues to be concerned with, as the process unit or plant would be shutting down.
A typical oil mist system uses 2 gallons of oil per 24 hours. A fully instrumented oil mist generator has a 9-gallon misting chamber and a 75-gallon bulk reserve. Many process plant installations include an additional 110-gallon bulk oil tank, thus providing an oil supply of approximately 200 days of continuous operation.
Figure 4. A gas blower lubricated by oil mist
Dry Sump or Pure Mist?
Dry sump or pure mist is the preferred lubrication method for most rolling-element bearings, including pumps, motors and pillow-block bearing applications. Pure oil mist can also provide superior lubrication over traditional oil sump or grease lubrication. Where there is no oil level in the bearing housing, oil mist is the only means of lubrication. The preferred flow of oil mist is through the bearings, side to side or top to bottom.
Pump and motor manufacturers are quite aware of oil mist systems, and most have designed their equipment for use with this type of lubrication. Current API standards also support the use of oil mist for equipment lubrication and preservation.
Technical Risks
Oil mist systems are relatively simple, operating at 0.73 pounds per square inch with a flow rate of 20-24 feet per second. With no moving parts to wear out or fail, many systems in the refining industry have exceeded 40 years of operation. Turnkey installations can be provided by the supplier. Training for operations and maintenance personnel normally is offered onsite, along with customer support and service. Routine maintenance contracts are common in most facilities.
Case Study
The Petronor oil refinery in northeastern Spain recently installed pure oil mist in the pillow block of a gas blower that originally was equipped with an oil console. The final conversion involved a dual pillow-block bearing arrangement for an air blower in the refinery’s sulfur unit. All the rotating machines in the plant were lubricated by oil mist except for this blower, which was a requirement of the plant licensor.
Since its startup, the blower had experienced multiple lubrication issues related to the oil console, such as oil cleanliness deficiencies and clogged oil injectors. The main pump also failed because the bearing’s pillow block had a very small oil volume and no constant-level oiler, so even a slight drop in the oil level put the pump and machine at risk.
After the system was studied by a design engineer, it was concluded that the oil console was unnecessary and too complicated to lubricate the pillow block. Oil mist, which already was installed on the surrounding machines, was determined to be the best option for simplifying the system and boosting the reliability of the blower.
During the upgrade, the oil console and related instrumentation were dismantled. The system’s current design (Figure 3) is much simpler. Now, the blower works much better than before, and the conversion cost was less than $6,000.
Lessons Learned
What can be learned from this case study is that reliability engineers often need to question the original design of their lubrication systems and refute underlying assumptions to improve reliability. System designs frequently are complex without justification. Complicated systems do not always mean reliable systems. Finally, consider oil mist as a possible lubrication method based on its proven ability to reduce equipment failure rates while increasing availability and throughput.
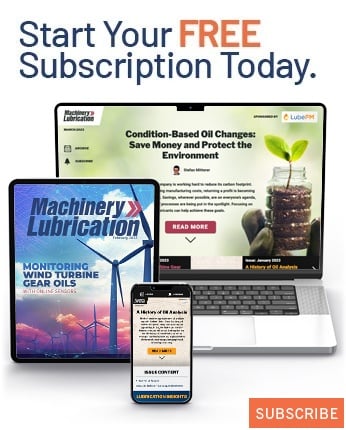