Bacterial contamination of large circulating oil systems in steam turbines, paper machines and similar systems is a growing and expensive problem.
The bacterial colonies, once established, will clog control systems, quickly degrade oil quality and oil performance and produce corrosive byproducts. If not detected early, the problem will manifest itself into expensive repairs, extended downtime and a significant expenditure of scarce resources.
As the United States steam turbine fleet ages and maintenance intervals are stretched, the problem is growing. Because steam turbines generate approximately 60 percent of the United States’ electrical power, the potential problem is significant.
This article presents a brief description of circulating oil bacterial contamination, problem recognition, types of lubricants and conditions that appear to be most susceptible, methods of treatment, and known methods to clean up and prevent bacterial contamination.
Figure 1. Naughton Plant
Bacterial Contamination in Oil - What Is It?
Bacterial contamination in crude oil and refined petroleum products has been well documented since the 1970s. The problem of bacterial contamination in steam turbine lube oil systems is increasing. Three classifications or types of bacteria typically encountered in petroleum products include:
-
Sulfate Reducing Bacteria (SRB) - This bacteria metabolizes sulfate and is anaerobic in nature.
-
Acid Producing Bacteria (APB) - This bacteria ferments sugars to acids (typically light organic acids) and is anaerobic in nature.
-
General Aerobic Bacteria (GAB) - This bacteria requires oxygen.
These three classifications of bacteria are prevalent in nature. With respect to human health and safety, none of these three bacteria classifications has been tested for human health hazards. It is possible, but not likely, that the GAB classification of bacterium could produce a bacteria strain that might prove pathogenic to a portion of the human population.
These bacteria need the following to survive and grow:
-
Water mixed into the oil; 500 ppm is sufficient (0.5 mL of water per Liter of turbine oil).
-
Organic material (carbon, nitrogen and phosphorous), supplied by the turbine lube oil hydrocarbon chains.
-
Oxygen; accelerates growth rates.
-
Optimum temperature (75ºF to 120ºF).
-
Stagnant/low flow and dark areas. Turbine lube oil systems abound with these types of protected locations.
-
Suspended particulates to serve as initial colonization or coalescing sites.
-
Emulsification of the oil to facilitate nutrient transport across the cellular boundary.
If any of the above is disrupted, the bacteria will not grow or survive. Obviously, the easiest environmental factor to influence is the water concentration in the oil.
Operational Signs and Symptoms
Bacterial contamination can be positively confirmed only by laboratory analysis. However, multiple signs and symptoms for operations and maintenance personnel are available. As the bacteria grow, they produce visible colonies of biomass. This biomass has approximately the same color as clear silicone room temperature vulcanizing (RTV) and looks like gelatin. One location where this biomass can be easily viewed is in the sight glass of a Turbo-tac or Kaydon Oil filtration skid.
Figure 2. Skid Sight Glass Bacteria Colony
Figure 2. Note the following in the sight glass from top to bottom: emulsified oil, oil water boundary, water layer and bacteria colony. This colony is primarily GAB.
Additional symptoms of bacterial contamination in a turbine lube oil system include:
-
Frequent plugging of filters with a jelly-like substance.
-
Sluggish or inadequate controls response, possibly resulting in a unit trip.
-
Plugging of control orifices or lines with a gooey, jelly-like substance.
-
Prolonged operation with water levels greater than 500 ppm.
-
Emulsified oil or an oily water mixture that will not readily separate.
-
Failure of the water demulsification test (ASTM D1401).2
-
Failure of the turbine oil foaming characteristics test (ASTM D892).2
-
Relatively rapid turbine oil oxidation as measured by the RPVOT test (ASTM D2272), especially if the oil has not been overheated.2
-
Isolated, concentrated rust spots on filter elements metal ends, turbine bearing components, etc.2
The bacterial contamination may also be visible in the bottom of drained turbine oil reservoirs (Figure 3).
Figure 3. Oil Reservoir
Figure 3. A boiler feed pump turbine lube oil reservoir. Note the rust production from the bacteria colonies. The lower right-hand corner of the picture shows a cleaned tank surface.
Figure 4. Filter Housing
Figure 4. The interior of a Kaydon unit that has been subject to heavy bacterial contamination and turbine oil with prolonged elevated water content.
Reynolds Number
The author presents 2,000 gpm as a target flow rate for the system flush. This represents a Reynolds number of 10,000+. It is customary to calculate the flow required to create turbulence to enhance a system flush by using the Reynolds number for turbulent flow. The Reynolds formula is: R= pVD/µ where:
p = fluid density
µ = fluid viscosity in centipoise
V = free stream fluid velocity
D = pipe diameter
The Reynolds number must be above 2,000 for system operating conditions to achieve a state of turbulence. As the distance from the centerline to the sidewall of the pipe increases, the relative fluid turbulence decreases, reaching roughly 50 percent fluid turbulence at 5 percent of the distance from sidewall to centerline. As the fluid reaches the pipe sidewall, fluid turbulence decreases to a point of laminar flow.
Particle removal performance depends on the lift and drag forces of the flush media, and the depth of the laminar sub layer in the stagnant film at the conduit wall. A particle completely submerged in the laminar sub-layer is impossible to flush from the system.”1
If the intention is to remove the remains of the dead biological material strictly through flushing, the Reynolds number would need to be high.
Confirm with Laboratory Analysis
Turbine lube oil bacterial contamination may be positively confirmed only through laboratory analysis. This type of analysis is usually performed by a microbiologist. Most oil analysis laboratories do not have this capability or technical expertise.
However, several of the major petroleum producers and refiners do have this type of technical expertise on staff. (Bacterial contamination is a major concern in the pipelines, tank farms and upstream side. PacifiCorp’s lubricant supplier was extremely helpful in this matter.)
The microbiological analysis will consist of incubating and growing colonies in different types of media and then analyzing for biomass activity/RNA/DNA. The laboratory will also attempt to perform activity level counts by the three different classifications of bacteria.
It is important to communicate with your lubricant supplier/microbiological laboratory to determine factors such as the types of samples, preservation requirements and sample locations. This is imperative for optimal analytical results.
Conditions that Favor Bacterial Colony Growth
The following conditions appear to provide optimal conditions for bacterial colony growth:
-
Prolonged water content greater than 500 ppm. Water is the necessary medium for the bacteria to live and grow. Even though their food source is the organic material in the turbine lube oil, water is required.
-
Relatively constant turbine lube oil temperatures over a prolonged period of time. As in food safety, bacteria growth can be inhibited by heating to elevated temperatures or storing at low temperatures.
-
Group I base stock. Group I base stocks tend to support more bacteria growth than Group II base stocks because of their higher aromatics and sulfur content. These compounds tend to tie-up the water in the oil and promote bacteria growth. Group II base stocks contain paraffins and naphthenes. They are free of aromatics and sulfur. They shed water faster than Group I base stocks, which minimizes bacteria growth, and they remove deposits from metal surfaces because of their polar nature.2
Clean-up and Treatment Methodology
Once bacterial contamination has established itself in the system, eradication can be difficult. The most effective method involves the following steps:
-
Remove the bacterially contaminated oil and send it off-site for use as fuel oil. It is important that in-plant transfer piping not be used during the removal of the contaminated oil. This will minimize the potential for spreading the problem to other components.
-
Inspect and clean the lube oil system. This involves disassembly and cleaning of major components. Specific attention should be paid to the reservoirs and filter housings.
-
High-volume /high-temperature oil flush. Utilize a new flush oil (do not use the old oil as flush oil) recommended by your lubricant supplier and perform a high-volume/ high-temperature flush. The oil temperature should be at 160°F minimum and flow rate should exceed 2,000 gpm for a 4,000-gallon turbine lube oil system (achieving a Reynolds number greater than 10,000 is desired). After the flush is complete, dispose of the flush oil as in step 1 above. This flush should also use high-quality, full-flow filtration capable of at least 3 micron at Beta>200. A before-and-after photo of the flush oil illustrates the cleaning that can be accomplished (Figure 5).
-
Perform a final inspection and cleaning of the reservoir and any other accessible components. Cleaning should follow the lubricant manufacturer’s instructions. The use of cleaning solvents or detergents is generally not recommended.
-
Refill with new oil. When refilling, utilize new hoses and fill directly to the reservoir from the transport unless the plant transfer piping is known to be clean and free of bacteria. Install new filter elements and place all filtration components in service. Ensure that the new oil is dry - less than 500 ppm water content.
-
Add a recommended biocide to the lube oil. Consult with your lubricant manufacturer for the best application. Test the new oil doped to the recommended biocide level to determine baseline data for: RPVOT, acid number, demulsification, foaming, viscosity, ASTM and color.2
![]() |
|
Flush Oil from the Transport
|
Flush Oil After
Three Days High-Volume/ High-Temperature Flush |
Figure 5. Turbine Flush Oil, Before and After
|
Keep in mind some important “dos and don’ts”:
-
Do not add biocide to the oil without performing any of the other activities. The biocide will kill the bacteria and release a tremendous biomass that will plug filters, control lines, etc. The plugging may be so complete that removal by flushing will be almost impossible.2
-
Do add biocide to the oil when the system is operational and after the system has been thoroughly cleaned, flushed and filled with new oil. Read and follow all precautions.
-
Do use an oil flush contractor that has state-of-the-art, engineered, high-volume pumping and filtration equipment. During the flushing process, it is important that the biomass and other contaminants that sustain the bacteria are kept in suspension and captured by the filtration equipment.
-
Do write a detailed specification and contractual document for the high-volume/high-temperature flush.
-
Do not cross-contaminate other plant systems with bacterially infected oil. Remember contamination control - utilize your microbiologist/laboratory to provide basic instructions in this concept.
-
Do assume that other plant lubrication systems are contaminated with bacteria and treat with biocide. Ensure that the biocide is compatible with these oil types.
Prevention of Bacterial Contamination
Prevention of lube oil bacterial contamination is relatively simple and straightforward: Keep the water in the oil to less than 500 ppm.
Other factors that will help prevent bacterial contamination include:
-
Utilize turbine oil/circulating oil formulated from Group II base stock.
-
Minimize the formation of stagnant water in separator sight glasses.
-
Maximize filtration, maintain low ISO particle counts. The bacteria need water to grow but they also need a coalescing site to start their colonies.
-
Perform daily “clear and bright” inspections.
-
Maintain an appropriate biocide dosage level if bacterial contamination has been identified and subsequently cleaned.
References
- Fitch, E.C. Fluid Contamination Control, 1988 p. 113.
- Author’s professional experience on multiple steam turbines over the past 20 years.
Acknowledgments
The author would like to thank Gary Jenneman and Ted Naman of ConocoPhillips for their contribution to this article.
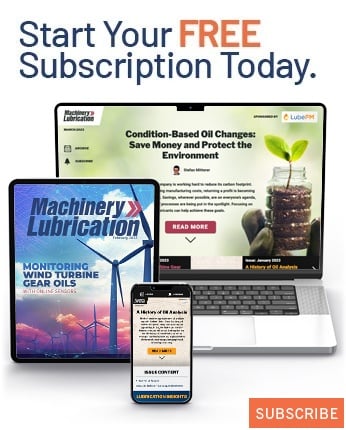