Why do oils appear to darken in clear, outdoor constant-level oilers? Is this a cause for concern?
Extended exposure to sunlight can cause oil to suffer accelerated oxidation and may lead to shortened drain intervals. On a molecular level, the long chain lubricant hydrocarbon reacts with oxygen in the presence of ultraviolet (UV) radiation from the sun.
As a result, it forms chromophores - conjugated aldehydes, ketones and esters. These absorb visible light to appear yellow at low concentrations and brown at higher concentrations after extended exposure to sunlight. To avoid this situation, one should protect the exposed oil from the ultraviolet energy in direct sunlight.
Product |
Acid Number
ASTM D974 |
Viscosity @
40°C cSt ASTM D445 |
Oxidation Induction
Time by PDSC Minutes 190°C ASTM D6186 |
Rotating Pressure
Vessel Oxidation Minutes ASTM D2272 |
A - new |
0.07
|
30.19
|
19
|
1,707
|
A - aged |
0.11
|
30.21
|
11
|
916
|
A - aged (glass) |
---
|
30.18
|
---
|
---
|
B - new |
0.04
|
29.81
|
10
|
367
|
B - aged |
0.07
|
28.88
|
13*
|
409
|
C - new |
0.07
|
30.18
|
22
|
1,840
|
C - aged |
0.11
|
30.27
|
22
|
1,530
|
Hydraulic new |
0.1
|
43.78
|
17
|
566
|
Hydraulic aged |
0.13
|
43.94
|
17
|
474
|
Table 1 A = Group II turbine oil with R&O additive package B = Hydrotreated (Group I) with R&O additive package C = “Carefully selected base oil” (as worded on product description) with R&O package D = Highly refined base stock (as worded on product description) with antiwear package * Considered to be within the reproducibility of the test method |
Analysis
The ultraviolet portion of the sunlight spectrum has shorter and higher energy wavelengths than visible or infrared portions. Upon direct exposure, UV rays can break chemical bonds and damage skin, plastics and mineral oil-based lubricants. The ozone layer in the stratosphere absorbs 99 percent of the UV rays coming from the sun. The remaining one percent can cause damage unless UV stabilizers are added to skin creams and plastics or the exposed object is shaded.
Some plastics are inherently stable to UV rays, such as the butyrate reservoirs in various gravity feed lubricators and polyethylene terephthalate (PET) sample bottles, however they do allow UV radiation to pass through, causing damage to the contained hydrocarbon fluid.
A simulation of reported dark turbine oils in outdoor gravity feed reservoirs was performed by placing various turbine oils, including a synthetic, in PET bottles in outdoor sunlight for five days. The increase in color can be seen in Figures 1 through 5. Turbine oil A was also exposed to sunlight in a glass bottle. The change in viscosity and color were essentially the same between glass and plastic.
![]() |
![]() |
||||
|
Figure 2. Fourier Transform Infrared (FTIR) Analysis of Turbine Oil A. Red = aged sample, Blue = fresh sample. Notable change is the peak at ~ 1688 cm-1 wavenumbers. This increase indicates some change in nitration levels.
|
||||
![]() |
Figure 3. FTIR Analysis of Turbine Oil A. Red = aged sample, Blue = fresh sample. Note there is little change in the level of phenolic antioxidant additives in the FTIR spectrum. Area of interest is at ~ 3640 cm-1 wavenumbers. This suggests the decrease in the Rotating Pressure Vessel Oxidation Test (RPVOT), Table No. 1 is due to a degraded amine additive at a wavenumber the FTIR cannot characterize. |
![]() |
![]() |
||||
|
Figure 5. FTIR Analysis of Turbine Oil B. Red = aged sample, Black = fresh sample. Note there is little change in the level of phenolic antioxidant additives in the FTIR spectrum. Area of interest is at ~ 3640 cm-1 wavenumbers. This oil had a steady oxidation stability value using RPVOT (Table No. 1).
|
||||
![]() |
![]() |
||||
|
Figure 7. FTIR Analysis of Turbine Oil C. Green = aged sample, Red = fresh sample. Note there is little change in the level of phenolic antioxidant additives in the FTIR spectrum. Area of interest is at ~ 3640 cm-1 wavenumbers. This suggests the decrease in oxidation stability is due to a degraded amine additive at a wavenumber the FTIR cannot characterize.
|
||||
![]() |
![]() |
||||
|
Figure 9. FTIR Analysis of Hydraulic Oil. Red = aged sample, Blue = fresh sample. Note there is little change in the level of phenolic antioxidant additives in the FTIR spectrum. Area of interest is at ~ 3640 cm-1 wave-numbers. This oil had a steady oxidation stability value using RPVOT (Table No. 1).
|
Oxidation Test Methods
Degradation is observed by small increases in acid number, viscosity and in some cases, a substantial decrease in oxidation resistance through the use of Pressurized Differential Scanning Calorimetry (PDSC) and Rotary Pressure Vessel Oxidation Test (PRVOT). With PDSC, the sample is subjected to 500 PSI of oxygen and isothermally heated.1
As the onset of oxidation occurs, there is a phase change in the base oil that is characterized by an exothermic reaction, considered to be the onset of oxidation time. With RPVOT, the sample is subjected to 90 PSI pure oxygen purge in a pressure vessel containing a copper coil and moisture catalyst, and heated to 150°C.
The point at which pressure stabilizes after reaching 150°C marks the initiation of test timeline. Oxygen pressure in the vessel decreases with the onset of oxidation. The test concludes once the pressure drops by 25 PSI. The test duration is noted in minutes.2
These same samples did not show any color change when exposed to indoor fluorescent light or sunlight coming through a UV-protected glass window.
Conclusion
Ultraviolet light can damage lubricants in a short period of time. The first sign of damage in this study was the oxidation resistance of the oil. This may seem all right if the system is a once-through drip lubricant where there is no need for high levels of oxidation stability. However, if the oil feed system is used as a constant leveler for a small reservoir, one may be adding bad oil to good oil!
References
- Using Calorimetry to Measure Motor Oil Remaining Useful Life
- Looking Forward to Lubricant Oxidation?
Editor’s Note:
This was originally published in Lube Notes, a publication of the Electric Power Research Institution.
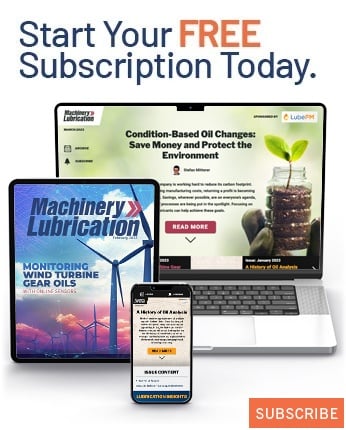