Aggressively controlling particle contamination in lubricants and fluids is one of the best strategies for extending machine life. Use this calculator to get an idea of just how much longer your equipment will last when you maintain cleaner oil levels.
Using a Proactive Maintenance Approach to Extend Machine Life
According to major industries throughout the world, it’s time to throw out your old ideas on machine maintenance. The cost-saving trend is toward a maintenance program that targets the root causes of machine wear and failure. Predictive and preventive maintenance methods are out: proactive maintenance is in.
Why? Because proactive maintenance methods are currently saving industries of all sizes millions of dollars on machine maintenance every year. This concept of saving large amounts on maintenance, however, may be tough for some to grasp. According to DuPont, “maintenance is the largest single controllable expenditure in a plant: In many companies it often exceeds annual net profit.”1 Add to this the fact that up to 90% of some companies’ maintenance work involves expensive (ad productivity-killing) breakdown repair, and you can easily see the predicament.
The problem of costly maintenance has truly reached a serious level, but as some companies have found out, and more come to realize every day, their maintenance costs can be cut drastically by establishing a “proactive” line of defense.
Getting to the Root of the Problem
When it comes to the life of a machine, whether it’s a lawn mower or a 1,000 h.p. bulldozer, cleanliness counts. Laboratory and field tests show that more than any other factor, fluid contamination is the number one culprit of equipment failure – even the most microscopic particles can eventually grind a machine to a halt.
Yet, the accepted methods currently being used to combat machine damage are based on either detecting the warning signs of failure once they’ve already begun (predictive) or regular maintenance according to a schedule rather than the machine’s true condition (preventive. No discipline has previously taken the micro view on machine damage – concentrating on the causes instead of the symptoms of wear.
Proactive maintenance is that discipline, and it is quickly being recognized worldwide as the single most important means of achieving savings unsurpassed by conventional maintenance techniques.
Proactive Maintenance vs. Preventive/Predictive
Imagine being able to pinpoint and eliminate a disease long before any symptoms occur in your body. It would save you money in doctor bills and keep you out of the hospital in the long run. This it the advantage of proactive maintenance over predictive and preventive maintenance.
Proactive maintenance commissions corrective actions aimed at the sources of failure. It is designed to extend the life of mechanical machinery opposed to 1) making repairs when often nothing is broken, 2) accommodating failure as routine and normal, and 3) preempting crisis failure maintenance in favor of scheduled failure maintenance – all of which are characteristics of the predictive/preventive disciplines.
Preventive maintenance, when used correctly, has been shown to produce maintenance savings in excess of 25%, but beyond this its benefit quickly approaches a point of diminishing return. The guess work involved simply renders it inefficient. According to a Forbes magazine article, one out of every three dollars spent on preventive maintenance is wasted. And a major overhaul facility reports that “60% of hydraulic pumps sent in for rebuild had nothing wrong with them” – a prime example of the disadvantages of performing maintenance to a schedule as opposed to the individual machine’s conditions and needs.
Where preventive maintenance fails in efficiency, predictive maintenance (also known as condition monitoring) offers improvement. This method involves the use of real time or portable instruments such as vibration, infrared and wear-debris monitors, to recognize the symptoms of impending machine failure. Predictive maintenance is more of an early warning technique to detect small amounts of damage before they lead to “catastrophic” failure.
While effective to a degree, neither preventive nor predictive maintenance is geared to detect the most common and serious culprit: contamination. Therefore, the first logical step to proactive maintenance is the implementation of a strict contamination control program for lubrication fluids, hydraulic fluids, gear oils and transmission fluids. It’s a strategy that receives support from industry and educational institutions alike:
- According to the bearings division of TRW, “contamination is the number one cause of bearing damage that leads to premature removal.”2
- According to Caterpillar, “dirt and contamination are by far the number one cause of hydraulic system failures.”3 Case Corporation states that “one thing holds true about hydraulic systems: The systems must be kept clean – spotlessly clean – in order to achieve the productivity they’re capable of.”4
- Massachusetts Institute of Technology states that “six to seven percent of the Gross National Product is required just to repair the damage caused by mechanical wear.”5 Wear occurs as a result of contamination.
- Oklahoma State University reports that when fluid is maintained 10 times cleaner, hydraulic pump life can be extended by 50 times.6
Human Health vs. Machine Health
Many parallels can be made between maintaining the health of a human body and maintaining the health of a mechanical system. Both are fluid-dependent systems, and both are in grave danger when those fluids are carrying high levels of contamination.
Success Stories in Contamination Control
Clearly, it’s cheaper and healthier to maintain a controlled approach to maintenance, whether you’re referring to a human or machine. But how does that translate into real savings? Industries use hydraulic systems, roller bearings and diesel engines have reported their successes while using the proactive maintenance approach.
After Nippon Steel (one of the world’s largest steel mills) implemented a contamination control program plantwide, involving improved filtration and rigorous fluid cleanliness monitoring, pump replacement frequencies were reduced by one fifth, and cumulative frequency of all tribological failures (i.e. failures relating to wear and contamination) was reduced to one tenth.7
International Paper Company reported nearly a 90% reduction in bearing failures in just six months after they implemented improved filtration and contamination control in their Pine Bluff, Arkansas, paper mill.8
AC Delco Division of General Motors tested Detroit Diesel Allison (DDA) engines and found an eightfold improvement in wear rates and engine life with lower lube oil contaminant levels. In a related study on both diesel and automotive engines, General Motors reported, “compared to a 40-micron filter, engine wear was reduced by 50% with 30-micron filtration. Likewise, wear was reduced by 70% with 15-micron filtration.”9
What Particles Mean and Why They Need to Be Monitored and Controlled
With the widespread use of plant-level particle counters, maintenance organizations are increasingly more sophisticated and skilled in the management and control of oil cleanliness. This has led to the discovery of a host of new tactics and practices in combining the particle counter with other important onsite oil analysis tools and methods; many unheard of just a few years ago.
Contamination can be defined as any unwanted substance or energy that enters or contacts the oil. Contaminants can come in a great many forms, some are highly destructive to the oil, its additives, and machine surfaces. It is often overlooked as a source of failure because its impact is usually slow and imperceptible yet, given time, the damage is analogous to eating the machine up from the inside out. While it is not practical to attempt to totally eradicate contamination from in-service lubricants, control of contaminant levels within acceptable limits is accomplishable and vitally important.
Particles, moisture, soot, heat, air, glycol, fuel, detergents, and process fluids are all contaminants commonly found in industrial lubricants and hydraulic fluids. However, it’s particle contamination that is widely recognized as the most destructive to the oil and machine. This explains why the particle counter is the most widely used instrument in oil analysis today. And, the central strategy to its success in reducing maintenance costs and increasing machine reliability is proactive maintenance.
How to Implement Proactive Maintenance
While the benefits of detecting abnormal machine wear or an aging lubricant condition are important and frequently achieved with oil analysis programs, they should be regarded as low on the scale of importance compared to the more rewarding objective of failure avoidance. This is achieved by treating the causes of failure, not simply the symptoms. And,is is the foundation of the popular practice known as proactive maintenance. In fact, the only effective way to obtain simple solutions to complex machine maintenance problems is through proactive maintenance.
Whenever a proactive maintenance strategy is applied, three steps are necessary to insure that its benefits are achieved. Since proactive maintenance, by definition, involves continuous monitoring and controlling of machine failure root causes, the first step is simply to set a target, or standard, associated with each root cause. In oil analysis, root causes of greatest importance relate to fluid contamination (particles, moisture, heat, coolant, etc.).
However, the process of defining precise and challenging targets (e.g., high cleanliness) is only the first step. Control of the fluid's conditions within these targets must then be achieved and sustained. This is the second step and often includes an audit of how fluids become contaminated and then systematically eliminating these entry points. Often better filtration and the use of separators are required.
The third step is the vital action element of providing the feedback loop of an oil analysis program. When exceptions occur (e.g., over target results) remedial actions can then be immediately commissioned. Using the proactive maintenance strategy, contamination control becomes a disciplined activity of monitoring and controlling high fluid cleanliness, not a crude activity of trending dirt levels.
Finally, when the life extension benefits of proactive maintenance are flanked by the early warning benefits of predictive maintenance, a comprehensive condition-based maintenance program results. While proactive maintenance stresses root-cause control, predictive maintenance targets the detection of incipient failure of both the fluid's properties and machine components like bearings and gears. It is this unique, early detection of machine faults and abnormal wear that is frequently referred to as the exclusive domain of oil analysis in the maintenance field.
Managing Particle Contamination in Lubricants
There is no single property of lubricating oil that challenges the reliability of machinery more than suspended particles. It would not be an exaggeration to refer to them as a microscopic wrecking crew. Small particles can ride in oil almost indefinitely and because they are not as friable (easily crumbled) as their larger brothers, the destruction can be continuous. Many studies have shown, with convincing evidence, the greater damage associated with small particles. Still, most maintenance professionals have misconceptions about the size of particles and the associated harm caused.
These misconceptions relate to the definition people apply to what is clean oil and what is dirty oil. And, it is this definition that influences the setting of appropriate target cleanliness levels for lubricating oils and hydraulic fluids. The process is not unlike a black box circuit. If we want a change to the output (longer and more reliable machine life) then there must be a change to the input (a lifestyle change, i.e., improved cleanliness). For instance, it’s not the monitoring of cholesterol that saves us from heart decease, instead it's the things we do to lower the cholesterol. Therefore the best target cleanliness level is one that is a marked improvement from historic levels.
![]() |
While there are numerous different methods used to arrive at target cleanliness levels for oils in different applications, most combine the importance of machine reliability with the general contaminant sensitivity of the machine to set the target. This approach is shown in Figure 1. The Reliability Penalty Factor and the Contaminant Severity Factor are arrived at by a special scoring system that is included with the Target Cleanliness Grid.
There are many expensive ways to achieve clean oil but experience has taught us the wisdom of contaminant exclusion–treating the cause not just the symptom. By effectively excluding the entry of contaminants and promptly removing contaminants when they do enter, the new cleanliness targets are frequently achieved. Concerns that filtration costs will increase are not often realized due to the greater overall control, especially from the standpoint of particle ingression.
Particle Counting—The "Invisible" Filter
Engineers learn that "controlled systems" are those that have feedback loops. In proactive maintenance this is the monitoring step, i.e., particle counting. If this is done on a frequent enough basis, not only is proactive maintenance achieved but also a large assortment of common problems can be routinely detected. As such, particle counting is an important "catch all" type test. Because of the obvious value, it is not uncommon to find organizations testing the cleanliness of their oils as frequently as weekly.
The activity of routine particle counting has a surprising impact on achieving cleaner oils. When the cleanliness of oil's are checked and verified on a frequent basis a phenomena known as the "invisible filter" occurs, which is analogous to the saying, "what gets measured gets done." Because a great deal of dirt and contamination that enters oils often come from the careless practices of operators and craftsmen, the combined effect of monitoring with a modicum of training can go a long way toward achieving cleanliness goals.
The following are common proactive and predictive maintenance uses of an onsite particle counter:
Proactive Maintenance:
1. Routinely verify that in-service oils are within targeted cleanliness levels.
2. Check the cleanliness of new oil deliveries.
3. Quickly identify failed or defective filters.
4. Confirm that seals and breathers are keeping contaminants out.
5. Confirm that systems are properly cleaned and flushed after repair.
6. Confirm that new machines are cleaned and flushed before use.
7. Identify the use of dirty top-up containers and poor maintenance practices.
8. Identify the timing for filter cart use.
Predictive Maintenance:
1. Identify early-stage abnormal machine wear with quick confirmation by repeating.
2. Identify the location/source of abnormal wear by multi-point isolating methods.
3. Verify the effectiveness of corrective maintenance and botched repair jobs.
4. Monitor machine break-in wear generation.
5. Identify abnormal rust and corrosion products in the oil.
6. Assist in confirming machines are balanced and aligned.
7. Permit more "on-condition" laboratory oil analysis.
8. Serve as an effective screen for wear debris analysis.
There are many different types of automatic particle counters used by oil analysis laboratories. There are also a number of different portable particle counters on the market. The performance of these instruments can vary considerably depending on the design and operating principle. Particle counters employing laser or white light are widely used because of their ability to count particles across a wide range of sizes. Pore-blockage type particle counters have a more narrow size range sensitivity; however, they're also popular because of their ability to discriminate between hard particles of other impurities in the oil. When good procedures and practices are followed, both types of particle counters provide value and effectiveness in maintenance applications.
![]() |
Figure 2 shows how particle count trends vary depending on the machine application and the presence of an onboard filter. Because particle counters monitor particles in the general size range controlled by filters, equilibrium is usually achieved, i.e., particles entering the oil from ingression minus particles exiting from filtration will leave behind a steady-state concentration. When filters are properly specified and ingression is under control this steady-state concentration will be well within the cleanliness target. Systems with no continuous filtration, e.g., a splash-fed gearbox, the equilibrium is not effectively established (there is no continuous particle removal). This causes the particle concentration to be continuously rising. Still, contamination control can be achieved by periodic use of portable filtration systems like a filter cart.
![]() |
By combining the use of a particle counter with other onsite oil analysis tools, particle count trends can be more effectively interpreted. Figure 3 shows how particle count trends from a circulating industrial gearbox can be monitored and interpreted when ferrous density analysis is added as an exception test.
Ferrous density analysis instruments are sold by several suppliers and include DR ferrograph, Particle Quantifier, and Ferrous Particle Counter. Figure 4 shows how particle trends can be compared to viscosity trends to reveal a host of crankcase lubrication problems.
![]() |
Training—Key to Success
Like most activities in oil analysis and maintenance technology, success in particle counting and contamination control requires education and skill development. Unless maintenance professionals have an understanding of the purpose and goals of oil analysis and are literate in the language of oil analysis, they cannot be expected to carry out its mission.
This is accomplished through a liberal amount of training and education. And, this should not simply be concentrated on a single individual but should be spread about to all those that benefit from and contribute to machine reliability. In fact, training and education should occur at several different levels including craftsmen, operators, engineering, and management. Below are a few subjects for which seminars and training classes are generally available through Noria Corporation:
1. Lubrication fundamentals and their use
2. Mechanical failure analysis
3. Proactive maintenance and root cause analysis
4. Troubleshooting hydraulic systems
5. Lubrication and maintenance of bearings and gear units
6. Oil analysis fundamentals
7. Oil analysis data interpretation
8. Filtration and contamination control
9. Wear particle analysis machine fault detection
Once these fundamentals are in place, oil analysis can move forward enthusiastically, beginning with the development of its mission and goals. And, instead of indifference to oil analysis exceptions, rapid-fire corrections are
carried out and measures are taken to preempt their reoccurrence. In time, unscheduled maintenance becomes rare and oil analysis exceptions are few as the idealized machine operating environment becomes controlled.
Finally, as the many elements of oil analysis and proactive maintenance merge together into a cohesive maintenance activity, the benefits should not be allowed to go unnoticed. Unlike many applications of new technology, proactive maintenance seeks non-events as its goal and reward. These non-events include oil that continues to be fit-for-service, machines that don't break down, and inspections that don't need to be performed. This quiet existence is the product of a highly disciplined activity but, at times, can be misunderstood by the casual observer as unneeded. Therefore, the close association of the activities of proactive maintenance with the benefits of proactive maintenance must be measured, monitored, and displayed for all to view.
References:
- DuPont Advertisement
- Plant Services Magazine
- Heavy Equipment Maintenance Magazine
- Equipment Management Magazine
- MIT Tribology Publication
- BFPR Journal
- Nippon Steel Conference Report
- Pall Symposium Report
- SAE Technical Paper
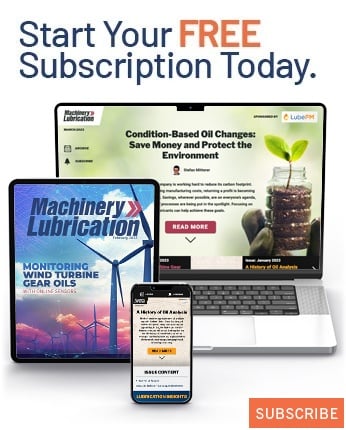