As a frequent instructor and consultant to major companies, I'm constantly amazed by the number of times I hear experienced maintenance professionals extol the virtues of "just change oil" to solve issues related either to contaminated oil or a nonconforming physical or chemical test (viscosity, acid number, additive content, etc.). Central to this belief is an inherent trust that by changing oil, the problem will disappear because new, pristine oil is added from a freshly opened barrel. But is this really the case?
Does New Oil Equal Clean Oil?
I'm sure many of you are aware that new oil is not always clean oil; and if you're not, you should be! Unless a lubricant supplier has taken special precautions while blending, filling the barrel (or other transfer vessel) and distribution, it is likely that the oil you are using is three to four ISO codes or eight to 16 times dirtier than recommended for critical applications. Likewise, many oils contain two to four times the maximum amount of water advisable for components sensitive to free and emulsified water.
Sample, Sample, Sample!
But the problem goes way beyond the cleanliness and dryness of new oils. To illustrate my point, I was recently made aware of two situations that if I were a maintenance manager, would result in a few sleepless nights. The first involved a routine oil sample taken from a gear reducer that showed a drop in phosphorus levels from 300 ppm to just a few ppm in the space of a few months. After assessing the possible causes, I asked my client if he had recently changed the oil, thinking perhaps the wrong oil had been added or a formulation change had occurred. Sure enough, the oil had been changed a few weeks prior, but the same brand and grade was used. My immediate response was to sample the new oil barrel. Imagine the surprise when no additive elements were found in the new oil sample oil and the barrel labeled as a formulated ISO VG 320 gear oil was in fact just pure base oil, with no additives!
The second situation is the polar opposite of the first and was relayed to me by a lube technician attending a public seminar I was teaching. In this case, the lube tech - a careful man by nature - was topping off a gearbox using a top-off container recently filled from a barrel of oil. However, when he was just about to pour the new oil into the machine, the tech observed a strange color, smell and consistency to the oil. After deciding not to use the oil, the technician referred the problem to his supervisor, who was able to determine that what came out of the new barrel of oil was a 100-percent pure additive package, with essentially no base oil.
The point of these two examples - both of which are true - is not to cast doubt or in any way suggest that lubricant suppliers or distributors are negligent in their practices, but rather to emphasize that in lubricant manufacturing, blending and distribution - like any other process where human interaction occurs - mistakes can and do happen. Imagine the hundreds of thousands of barrels of oil delivered each year, and the statistical probability of something going wrong with at least one of these barrels.
Quality Assurance
So how can you avoid becoming a victim of these rare but serious mistakes? The simple answer is to develop your own quality assurance (QA) program for all new oil delivered to the plant, or at least for oils used in critical applications (such as turbo-generator, paper machine circulating systems and rolling mill gear box central lube systems). For bulk oil deliveries, this is a simple process: each batch (bulk delivery) should either be sampled upon receipt and not used until the results are confirmed, or a QA certificate should be provided by the lubricant supplier or distributor showing the appropriate physical and chemical properties for the batch based on a QA sample taken after formulation (unfortunately this won't weed out mistakes due to the distribution process).
The problem is a little trickier for barrels. Testing each barrel can be a daunting (and costly) endeavor unless onsite oil analysis is available, but depending on your tolerance for risk, performing such tests could be beneficial. In each case, the properties for a given application (dryness, cleanliness, viscosity, additive content) should be tested and validated to be within acceptable ranges.
Just a Precaution
Many progressive companies can and do set up a process involving the quarantine of new oil deliveries before the results of the QA samples are confirmed. Only then is the new oil barrel put into circulation. Perhaps many of these are companies that have learned the hard way, and recognize the potential for a critical mistake in the lubricant procurement process.
While a formal QA program may not work for everyone - or every oil - my advice is to consider what a single mistake might cost your company and whether you might be well served to take steps to identify potential problems early in the process, before becoming a graduate of the school of hard knocks.
As always, this is my opinion. I'm interested in hearing yours.
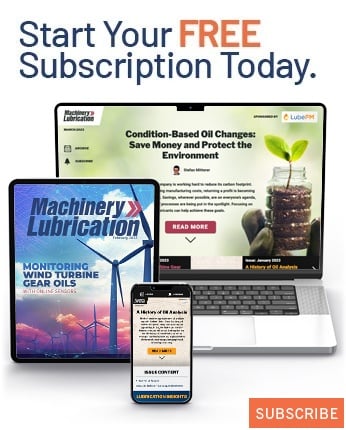