With the movement to digital solutions for tracking and managing most decisions that are made in reliability and maintenance, an area that is often left out is lubricant selection. This is the most fundamental step in a lubrication program: selecting the proper lubricant for the application at hand. Be that as it may, the task of choosing lubricants is often relegated to the lube tech, operator, maintenance personnel or whoever happens to be next to the equipment in need of lubricating. Seldom is there much emphasis put on the selectionand even less emphasis is placed on a mechanism to track how well we are doing in this realm.
Since lubricant selection impacts many facets of equipment operation, there are many ways in which we can track the performance of our lubricant selection process. Some methods can be leading, some lagging, but all are focused on giving us insight into the process as a whole.
Often, the selected lubricant is either the cheapest one available or whatever the OEM recommends for the machine. Either case can lead to a state of excess or a state of waste, which ultimately needs to be avoided. Therefore, we need to have some information to help prepare us to track the process.
Leading Indicators
Let's begin with some leading indicators for our lubrication selection process - leading indicators meaning that we are tracking items that are intended to get our desired result. For example, if you are dieting, caloric intake would be a leading indicator of weight loss. For selecting the ideal lubricant, a few items we may track are:
Lubricants that match/exceed the OEM specification
OEMs often spec a lubricant based upon the design of their equipment. We need to ensure the lubricant we select meets or exceeds the spec from the OEM and is adjusted based on our unique environment and application. A lubricant that doesn't meet these standards could result in sub-optimum performance.
Number of lubricants on-hand
This could be viewed as a way to track the consolidation of lubricants in the plant. Ideally, we minimize the lubricants, keeping only on hand what we need to operate without sacrificing the needs of the equipment. By tracking the number of lubricants and even the number of applications using that lubricant, we can help keep our consolidation efforts in place.
Age of lubricants in storage
Lubricants all have a shelf life; ideally, we will utilize them before they go bad in storage. By tracking their age, we can help adjust our inventory levels. This also aids in our consolidation efforts by converting some equipment over to other lubricants (where applicable) to improve inventory turnover.
Lubricant purchase costs
As with most items, cost shouldn't be the only factor, but it still needs to be considered. Develop a matrix of cost against the performance of the lubricant to get a better sense of if it is worth the added cost. Also, tracking purchases over a time period can help justify moving to a higher-performing lubricant (which will need to be changed less frequently).
(Side note: The lead time for delivery of lubricants is becoming a large issue due to supply chain disruption. While it may not require a long-term metric, some are using this as a criterion when selecting a lubricant right now. Having a dialogue with your supplier about lead time or volume on hand may help minimize any surprises in the future.)
Lagging Indicators
Lagging indicators track what just happened, meaning that they result from the action we are hoping to achieve. Using the same weight loss analogy, the number on the scale after you step on it is a lagging indicator. So is your waist size. If we are selecting the proper lubricant for the application, a few of the key metrics we might hope to track ar
Energy consumption
Lubricant selection has a direct impact on the energy consumption of a piece of equipment. Think about viscosity (which is only one of many properties that can impact this); if it is too high or too low, there will be an impact on energy. By tracking amp draw or kW hours of lubricated equipment, we can help dial in the selection and also recoup some money based on the lube program.
Operating temperature
The hotter something runs, the faster it breaks down. If the machine is working harder to churn through a lubricant, the temperature will rise. Some lubricants have lower internal friction and can help lower operating temperature. Similar to energy conservation, this metric can help with selection and serve as a leading indicator of equipment/lubricant failure.
Change intervals
Lubricants should be changed before they reach the end of their life. If lubricant properties are matched to the machine's needs, we should expect to see an increase in the change interval. It could also be a result of our lubricant analysis program to help set ideal change intervals.
Lubricant disposal
Looking at either the volume of lubricant disposed of or the cost of disposal provides a lagging metric of how well we are doing with lubricant change intervals, leaks, and subsequently, selection. Proper lubricants can help with all of these factors, and again, this cost can be directly affected by lubricant selection.
Checks and Balances
Simply setting metrics to track the process isn't enough - action has to be taken to achieve the desired results. For some organizations, the responsibility of lubricant selection doesn't fall to one person; rather, a committee is tasked with the process. While the goal is not to create bureaucracy for the sake of it, there needs to be a system of checks and balances to ensure lubricants aren't needlessly added or dropped from the inventory. It is common for industrial facilities to add equipment or update lines periodically, so the lubricant properties needed tend to change as well. Without keen oversight, your lubricant inventory can get out of hand. The goal is to create a process that is sustainable and that consistently gives us the desired result, which is to provide the proper lubricant to a piece of equipment that meets the needs of the equipment, has adequate life at an appropriate cost and can be delivered in a proper manner.
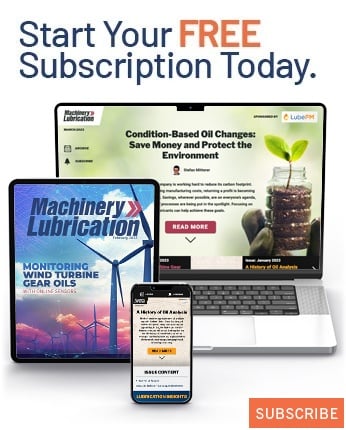