When touting the virtues of a well-designed and implemented lubrication program, we often advocate and prescribe a holistic approach. This is important because lubrication, or maintenance in general, is a chain of steps or sequence of activities designed to produce a positive end result, and the result is reliability.
Like any other chain, lubrication is only as good as its weakest link. This analogy can be applied to most components of the lubrication program including storage and handling, oil analysis, greasing bearings and inspection PMs. These components require multiple related activities to produce an end result, which can be diminished or eliminated by omitting or incorrectly performing one of the requisite activities.
The obvious question is how to identify and guard against these weak links. The answer is to audit the program to identify the problems, then document the procedures required to address them.
Contamination Control
A common component that fits this scenario is the storage, handling and application of lubricants. Controlling contamination in lubricated equipment is imperative for any lubrication program. One common and often overlooked source of contamination is new oil. If an oil sample is taken from a new drum of oil and tested for particle count, the results may be surprising.
Unless extraordinary steps are taken, new oil coming from drums is dirtier than even modest cleanliness standards for equipment will allow. Therefore, the new oil must be cleaned. This can be accomplished by filtering the new drum of oil with a filter cart prior to installation. However, this does not ensure the oil will be clean when it goes into service. What about the transfer container? What about the funnel? What about the application method?
I am often surprised to see the lengths people will endure to obtain clean new oil, then contaminate it by using a filthy oil can for transfer to the machine or pouring it through a dirty funnel. For this process to be effective, the oil must be clean when it is added to the machine and applied in a manner that prevents atmospheric contamination from entering the sump during transfer.
By examining the way lubricants are stored, transferred and applied to the equipment (chain of custody), the so-called weak links in the chain can be identified. Upon discovery, problems can be eliminated by defining the appropriate methods and documenting the best-practice procedures. Read Lubricant Quality - How Does the Chain of Custody Affect It? for more on this.
Inspection Procedures
Another common weak link I've observed takes place in routine PM inspections. Equipment inspections and condition monitoring are essential parts of a proactive maintenance strategy. While most plants have some form of routine inspection program, many do not employ procedures.
Additionally, some plants that do have inspection procedures do not have documented or formal processes to address abnormal conditions discovered during inspections. If an oil-lubricated component has a consistently low oil level that requires makeup oil, a documented process should be in place to address the problem.
I was recently in a plant that employed a number of central grease systems when I observed many broken grease lines. These broken lines would undoubtedly lead to bearing failures and possibly loss of production. After discussing this issue with plant personnel, I learned that although these machines were supposed to be inspected regularly, there was no system or procedure in place for reporting them other than by word of mouth.
Sampling
Oil analysis is possibly the most often compromised program due to one or more weak links in the process. For the program to be effective, good sampling methods, appropriate test slates and good data management which includes tracking historical data as well as establishing appropriate alarms and limits must be in place.
In this case, the common weak link is sampling. Without proper sampling methods, the value of oil analysis will be lost or severely diminished. The problem here lies in inconsistent and often invalid data. Unless you can take consistent, repeatable samples, it is impossible to establish useful alarms levels.
Additionally, sampling from a poorly chosen location, such as a gearbox drain port, may lead to false conclusions about the condition of the machine causing unnecessary work orders to be generated.
It's important to remember that it is often necessary to view the entire picture when making changes or improvements to a lubrication or maintenance program. To achieve positive results from any initiative, it is crucial to examine all of the steps in process. To ensure success, start by defining the desired result, identify the measures required to achieve that result, document the methods and finally, measure the results to identify any deficiencies.
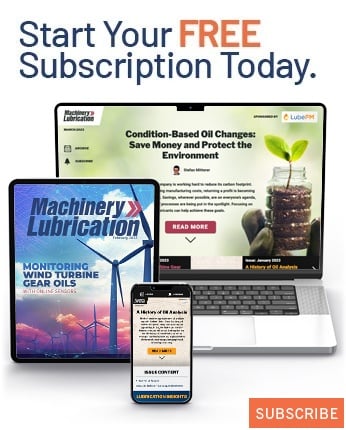